Incorporating H1 food grade lubricants into HACCP and GMP
- Like
- Digg
- Del
- Tumblr
- VKontakte
- Buffer
- Love This
- Odnoklassniki
- Meneame
- Blogger
- Amazon
- Yahoo Mail
- Gmail
- AOL
- Newsvine
- HackerNews
- Evernote
- MySpace
- Mail.ru
- Viadeo
- Line
- Comments
- Yummly
- SMS
- Viber
- Telegram
- Subscribe
- Skype
- Facebook Messenger
- Kakao
- LiveJournal
- Yammer
- Edgar
- Fintel
- Mix
- Instapaper
- Copy Link
Posted: 6 December 2019 | Andre Adam | No comments yet
Andre Adam, from FRAGOL AG, gives his insight into how food producers should incorporate food grade lubricants into their safety and hazard assessments in order to reduce the risk of food contamination.
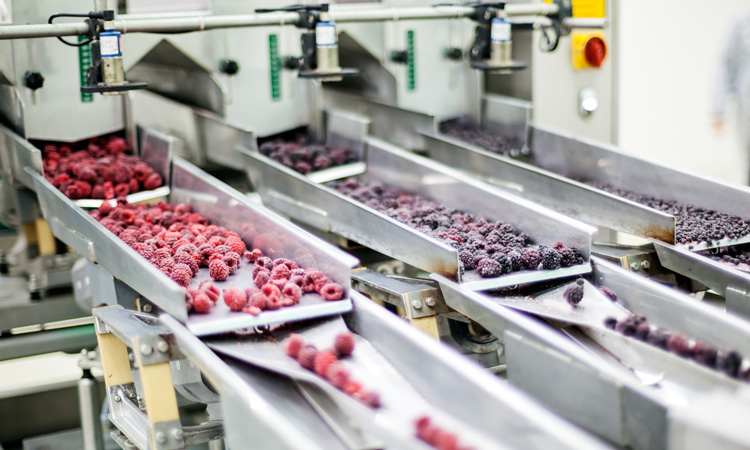
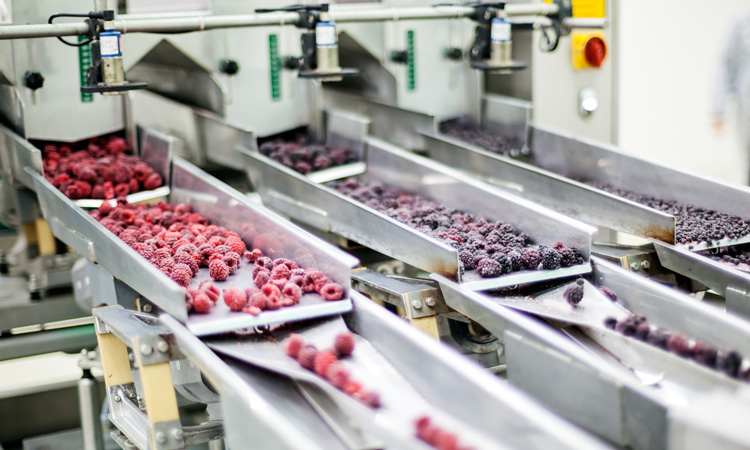
The use of H1 lubricants, registered by NSF, InS or 2Probity, should be common practice in any food producing plant, including the intermediate supply industry. The highly refined products, preferably produced under ISO21469, provide extra safety that is required for mechanised food production. The category H1 is based on the FDA 21CFR178.3750 and gives the maximum of lubricant present in the final food, such as mineral oil-based products at 10 part per million.
The rule here is that the lubricants used are for incidental food contact and not defined as a food additive. If a leakage occurs, immediate repairs should be initiated, and foodstuff should de disposed of when high concentrations of lubricant occur. The lubricant is considered a very safe product, but is not intended as an ingredient.
Analysis in production should be fast, cost effective and above all, reliable
If I focus here on the mineral oil-based lubricants – the most common – we are confronted with the question of how to verify the amount of lubricant in the final food. This is a major problem, as well as the need to analyse all components prior to working with them. Analysis in production should be fast, cost effective and above all, reliable
We also learned that the extraction methods, the analytical methods and the interpretation of the results were less than reliable
During the last three years, we learned from the many reports on MOSH and MOAH that mineral oil was found in food like pasta, milk powder and chocolate. These reports had negative effect on sales, and the reputation of the brands that were marked as ‘bad’. We also learned that the extraction methods, the analytical methods and the interpretation of the results were less than reliable. Same samples sent to different laboratories gave vastly different results. Overall, we can conclude that the data from analytics are an indication, but the data will not further inform us where the mineral oil hydrocarbons came from. For a food stuff producer, this is not helpful because the tests are difficult, unreliable, expensive and take way too much time.
What to do with lubricant in your plant
Changing to a mineral oil free product does little for the end result in a test done on the final food. MOSH and MOAH (mineral oil) can still be found originating from many other possible sources, including nature. Other lubricants base oils will show MOSH and additives can also be a source.
The best way is to determine how much lubricant oil is being used in a plant. Record all top-up (not oil change) and establish that there are no leaks to the plant floor. This would present a hazard due to the slippery surface that workers might encounter. Top up means it has gone somewhere – this could be evaporation – but also leaks into foodstuff.
The top-up will be minimal with modern lubricants. As such, this will enable you to calculate how much lubricant you added to your product and how much food you produced. It is clear that oil levels should be checked daily and under identical conditions, because heat will have an effect on the oil level.
Keep record of all oil top-up and with this you can show that you take responsible care and you can prove you are well below the 10 p.p.m. threshold for mineral oil. Realising that the highly refined mineral oils are proven to be safe, even though they contain MOSH and MOAH (the safe 1 and 2 ring PAC), you have at least the certainty that your production process contributed to a safe final product you intend to market.
About the author
Andre Adam is the International Sales Director at FRAGOL AG, a German based Specialty Lubricants developer and producer of private label products with focus on Food Safe lubricants and compressor and vacuum application fluids. Andre now has more than 35 years of experience in the lubricant industry working for Castrol, Petro-Canada and Anderol in many countries.
As Chairman of the H1 Global Food Lubricants Workgroup under the ELGI (as well as board member of the ELGI) and as contributor of CONCAWE-MOCRINIS work group, he continues to promote the interests of the lubricant industry in the food segment.
Related topics
Food Grade Lubricants, Food Safety, Health & Nutrition, Supply chain