Excellence in supply chain management
- Like
- Digg
- Del
- Tumblr
- VKontakte
- Buffer
- Love This
- Odnoklassniki
- Meneame
- Blogger
- Amazon
- Yahoo Mail
- Gmail
- AOL
- Newsvine
- HackerNews
- Evernote
- MySpace
- Mail.ru
- Viadeo
- Line
- Comments
- Yummly
- SMS
- Viber
- Telegram
- Subscribe
- Skype
- Facebook Messenger
- Kakao
- LiveJournal
- Yammer
- Edgar
- Fintel
- Mix
- Instapaper
- Copy Link
Posted: 28 June 2021 | New Food Magazine | No comments yet
New Food recently hosted a webinar in association with Aptean that addressed excellence in supply chain management for food and beverage businesses. During the session, Jack Payne shared insights with participants – some of which are highlighted here.
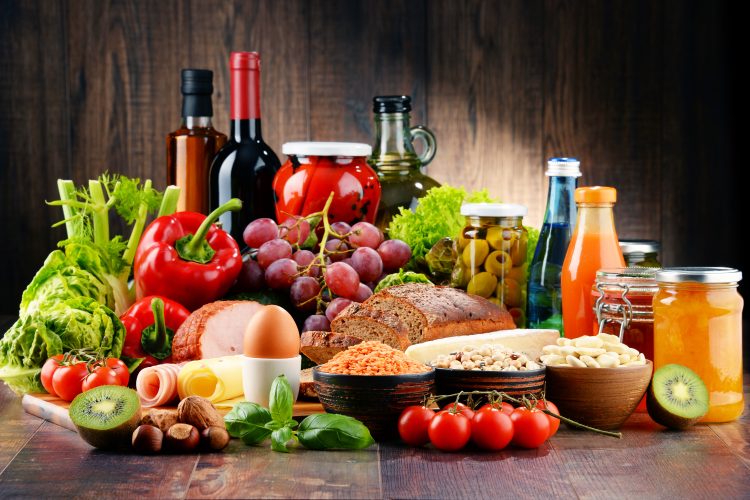
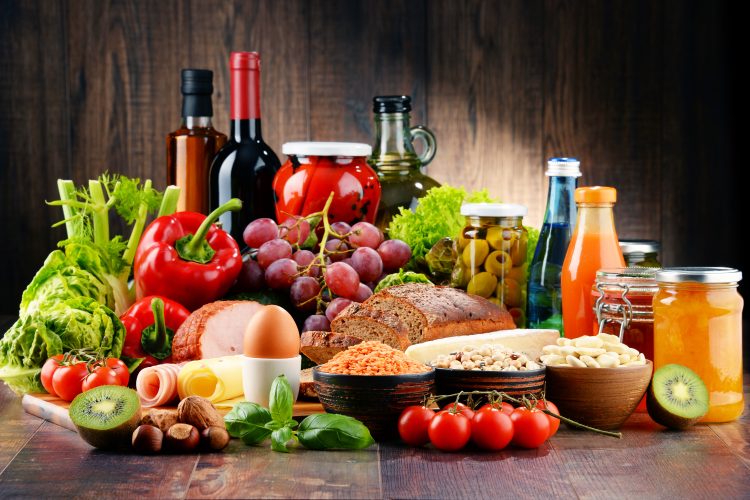
In a recent webinar, Jack Payne, Solution Consulting Director for Food & Beverage at Aptean, discussed trends in supply chain management, the importance of digital transformation and solutions built specifically for food and beverage companies, and how these can best be utilised to improve supply chain efforts.
Among the insights offered by Payne was the significance of changing consumer demands – cited as having the largest impact on the supply chain for food and beverage businesses – and the similarities between digital transformations and continuous improvement (CI) initiatives.
A major theme throughout the webinar was how vital it is that food and beverage businesses acknowledge the value of digital solutions for supply chain management, as the paperless, cloud‑based environments of these systems are fundamental to keeping pace in a competitive marketplace. Below, Payne summarises the key takeaways from his presentation, as well as some of his answers to questions fielded by the audience.
What are the benefits of moving to the cloud?
The move to cloud is something that’s gained traction in the last four to six years. Most of the new customers that we’re seeing in the food and beverage industry are electing to deploy on cloud, and there are a number of benefits and reasons for this.
One of these is business continuity; I’ve unfortunately talked to too many companies with on-premise systems that have experienced some kind of disaster or cyberattack that has impacted their business. In some of these scenarios, businesses recovered in a matter of days, but others took weeks or months.
Cyberattacks are becoming more prevalent – more than 50 percent of companies have suffered a cyberattack, and the prediction is that in 2021, a business will become the victim of a cyberattack once every 11 seconds. You should also consider that, from an economic standpoint, cloud deployment is a cheaper process than on-premise systems when you account for all the ancillary factors.
We see cloud as the future – and we’ve seen a lot of adoptions.
How long does a digital transformation take?
It’s not an overnight journey. The first step is taking inventory and analysing your existing foundation and backbone systems.
Do you need to upgrade your existing systems to be able to utilise the technology that comes with a digital transformation, or do you need to replace them?
This could take six months to over a year, but then as you start deploying technology, there’s going to be changes in culture and business processes. So typically digital transformation is a minimum two to three year process.
But it’s not that you will only start seeing the benefits after three years; you’ll experience the benefits along the journey.
Should I consider upgrading or replacing my current ERP system?
The first thing you need to do is look at what your enterprise resource planning (ERP) system currently offers. Does it meet your business needs? Does it have the technology capabilities to collect information digitally? Does it have the ability to provide analytics?
Most consultants in the industry would advise looking to improve what you have today rather than outright replacing it. However, if you have a system that doesn’t support what you need, that digital transformation is going to be a very difficult journey; you may have many delays and breakdowns along the way without that proper backbone.
So when it comes to upgrading or replacing, it must be assessed on a case‑by-case basis. I wouldn’t automatically say you should go and replace your system, but rather suggest looking at what you have and seeing if it can work. If you discover it can’t, it might need to be upgraded or replaced.
Related topics
Equipment, Food Safety, Processing, Supply chain, Technology & Innovation