Metal detectable plastics use in cleaning tools and utensils
- Like
- Digg
- Del
- Tumblr
- VKontakte
- Buffer
- Love This
- Odnoklassniki
- Meneame
- Blogger
- Amazon
- Yahoo Mail
- Gmail
- AOL
- Newsvine
- HackerNews
- Evernote
- MySpace
- Mail.ru
- Viadeo
- Line
- Comments
- Yummly
- SMS
- Viber
- Telegram
- Subscribe
- Skype
- Facebook Messenger
- Kakao
- LiveJournal
- Yammer
- Edgar
- Fintel
- Mix
- Instapaper
- Copy Link
Posted: 14 October 2016 | Debra Smith, Global Hygiene Specialist, Vikan | 3 comments
Global Hygiene Specialist at Vikan, Debra Smith describes the use of metal detectable plastics in cleaning tools and utensils.
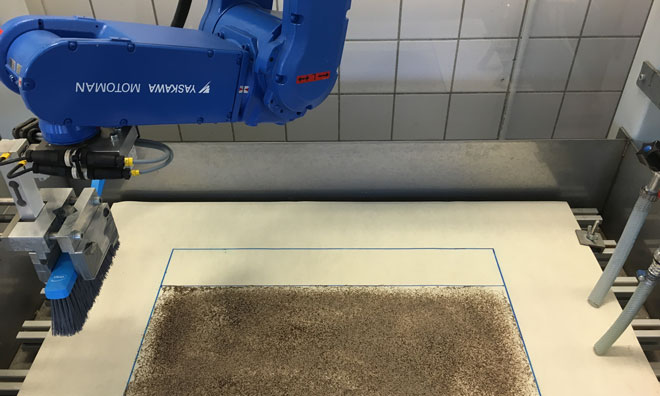
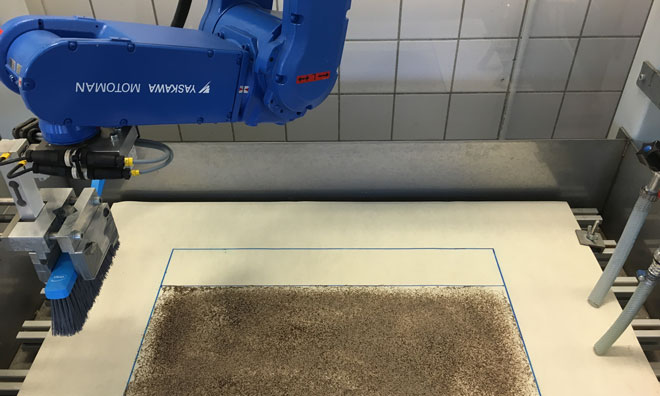
Foreign body contamination of foods can be a safety or quality issue, or both. Regardless, if a food is contaminated by a foreign body the repercussions for the food business can be expensive and damaging.
Metal detection is a well established and effective method of reducing the risk of metal fragments in commercial food products. Control of plastic foreign bodies is more difficult. Metal detectable plastics have been developed with the intention that metal detectors can also be used for their detection but how detectable are these plastics? Many food manufacturers are unaware that the metal detectability of any metal containing foreign body will depend on a number of factors, including the following:
- Metal content of the contaminant; both the quantity and type of metal
- Size of the metal containing contaminant
- Orientation of the metal containing contaminant
- The food product – size, composition
- Food packaging
- Speed of the conveyor belt
- Detector used
- Detector calibration.
Each of these interfering factors has an effect on the detectability of the metal containing contaminant and the interferences are often cumulative, as illustrated in Figure 1.
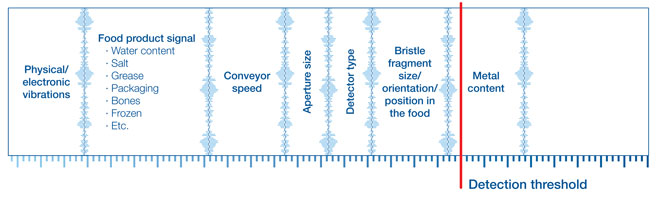
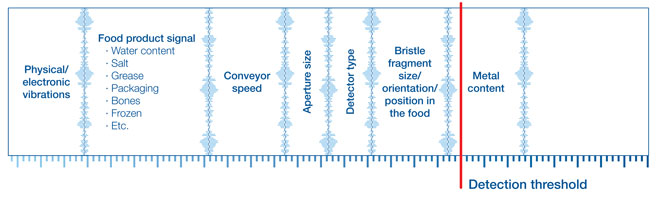
Figure 1: Factors affecting the metal detectable threshold
Consequently, metal detection systems do not give 100% security even with regard to the detection of totally ferrous metal objects. Additionally, metal detection systems cannot detect non-metallic items such as bone, glass, or stone.
The metal detectable plastics used in the construction of food industry standard utensils and cleaning equipment only contain a small percentage of metal detectable material. Consequently, metal detection systems only work if the fragments of this equipment are large enough to detect (given other detector limitations).
Most manufacturers of metal detection equipment will provide ‘calibration test pieces’, to check the function of the detector against ferrous and nonferrous metals. These are regularly used by the food manufacturer to verify the performance of their metal detection system. Some manufacturers of metal detectable plastic equipment will also provide a test kit that enables the food manufacturer to find out what size of metal detectable plastic can be detected by their detector/in their product.
However, very few do this. Research undertaken by Vikan, Denmark, to determine the metal detectability of a range of metal detectable plastics available to the food industry, show that not all are sufficiently detectable.
Detectability of metal detectable plastics used in the manufacture of cleaning tools and utensils
Initial investigations were conducted in collaboration with Detectronic, a Danish based metal detection system manufacturer.
An example of a metal detectable plastic test kit, as provided by some metal detectable plastic equipment manufacturers is shown in the header image. Figure 2 shows the results of the investigation.
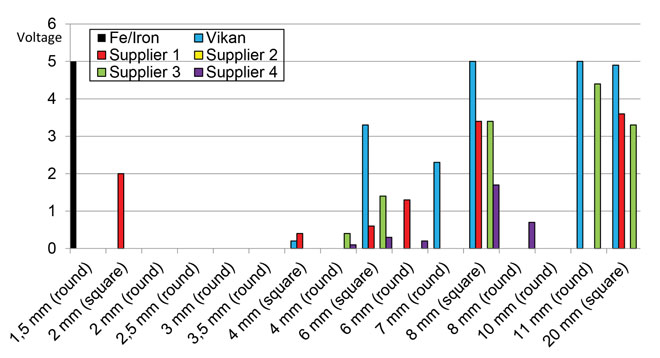
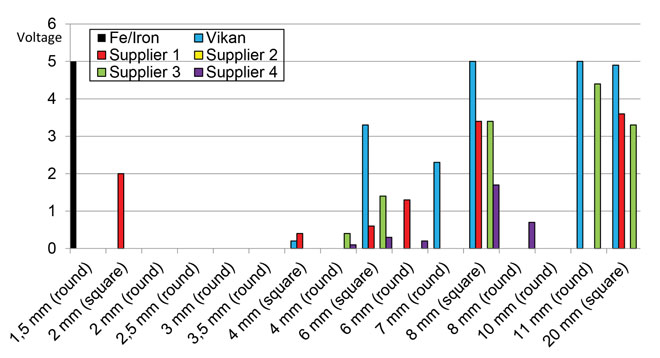
Figure 2: Metal detectable plastics test kit results
Results
The results demonstrate that, even without the additional interferences of product and packaging, the detectability of metal detectable plastics varies greatly. None of the samples from Supplier 2 were detectable and even the best detected metal detectable plastics (Vikan) needed to be over seven times the size of the iron sample to generate a similar reading, i.e. an 11mm round piece of metal detectable plastic was required to generate a similar detection signal to a 1.5mm round piece of iron.
Consequently, if the use of metal detectable plastic equipment is deemed necessary, the selection of appropriately metal detectable plastic equipment is essential to minimise the foreign body risk from this source.
Detectability of metal detectable plastic bristles
In a separate study Vikan sought to determine the metal detectability of metal detectable plastic bristles, as well as their durability and functionality, in terms of how well they clean.
In collaboration with Mettler Toledo, a multinational manufacturer of food industry metal detection systems, food industry standard metal detectable bristles were investigated with regard to their detectability using a Profile Advantage multifrequency Metal Detector, with and without the presence of a dry (packed granulated white sugar) food product and a wet (packed fresh chicken breast) food product.
Conclusion
Metal detectable plastic bristles were not detectable in the presence of food and packaging, as shown in Table 1. Additionally, to achieve a similar detection to that of a ferrous ball with a spherical diameter of 1.5mm, metal wire lengths of between 3mm and 9mm would be required, as shown in Table 2.
Currently, brushes with metal detectable plastic bristles are only available with bristle diameters of 0.35mm, 0.50mm and 0.60mm, i.e. much thinner than the metal wires assessed in Table 2.
It can be concluded, therefore, that even longer lengths of metal detectable plastic bristles would be required to achieve the same level of detection.
For example, using the data highlighted in Table 1 a metal detectable bristle with a cross-sectional diameter of 0.50mm and a length of 50mm gives an equivalent detection to that of a 1.8mm ferrous ball.
Durability of metal detectable plastic bristles
Tests to assess the break strength and elasticity of metal detectable and plastic bristles were performed by Zwick Roell, Germany, using a Zwicki 5kN bristle pull test apparatus.
Polyester (PBT) bristles were 68% stronger than elastic and metal detectable bristles, as shown in Tables 3a & b below:
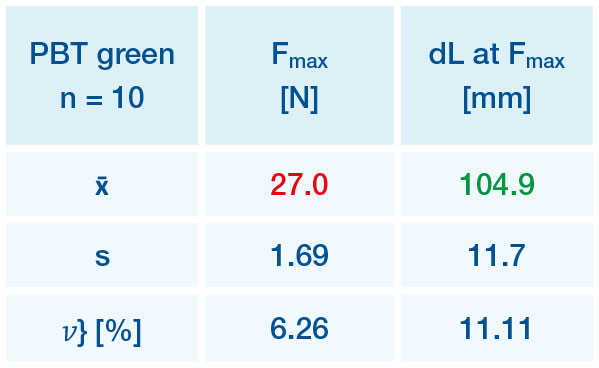
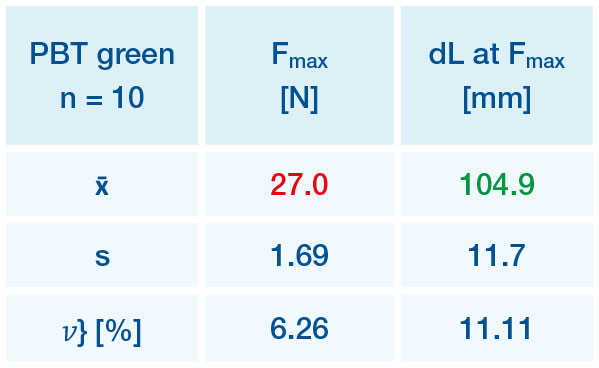
3a
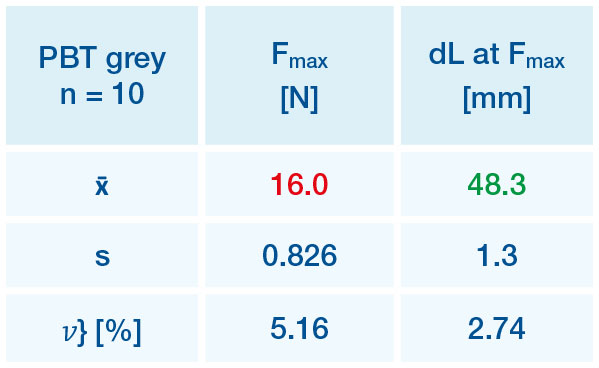
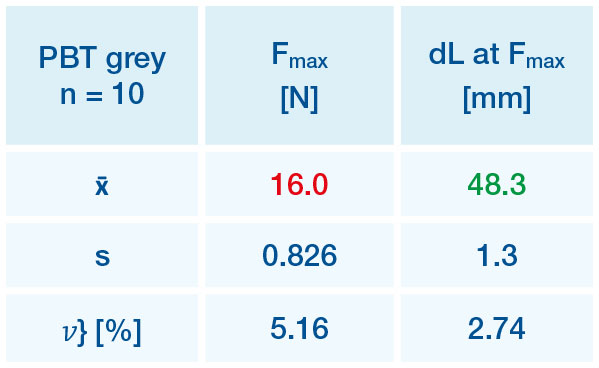
3b
Functionality of metal detectable plastic bristles
The ability of metal detectable bristled brushware to clean a surface of a wet (tinned chopped tomatoes) and a dry (mix of milk powder and ground coffee) food soil, was compared with that of a standard plastic bristled brush, using a robotic cleaning rig (Vikan, Denmark).
Conclusion
Based on visual assessment the metal detectable plastic bristled brush was no more effective at cleaning than the standard plastic bristled brush.
Discussion
Based on the findings of these investigations it seems unlikely that metal detectable plastic bristles would be detectable in a food product, especially given previously mentioned detector and product accumulative variances, and that the plastic fragments are likely to be small. To detect these small fragments the metal detector sensitivity would need to be set so high that most products would be rejected. The use of metal detectable plastic bristled brushes may, in fact, increase the risk of bristle contamination of food, due to their reduced strength and elasticity, and a perception that any metal detectable bristles will be controlled via the metal detector.
Additionally, metal detectable plastic bristled brushware offers no advantage over plastic bristled brushes with regard to cleaning efficacy. Currently, only relatively thick metal detectable plastic bristles are available, i.e., >0.35mm diameter. However, fine bristled brushes are more effective at removing fine powders, including some allergens. Consequently, the use of thicker bristled brushes may result in poor cleaning efficacy and, therefore, increase the risk to the business/consumer.
As an alternative to the use of metal detectable plastic bristled brushware, it is suggested that brushes are regularly inspected and replaced, in order to minimise the risk of foreign body contamination from this source, and that brushes of a contrasting colour to the food product be used to enable the plastic bristles to be seen more easily in the product. Additionally, the use of a brush that minimises bristle loss through good construction is advisable.
About the Author
Debra Smith has more than 30 years of food safety training and experience, as well as degrees in Applied Microbiology, Food Science and Nutrition. She is FSSC 22000 audit qualified, as well as being trained in Advanced Food Safety, and Intermediate HACCP. She has been Global Hygiene Specialist at Vikan for five years
Just what I was looking for. Thanks for sharing.
A well-informative article, thanks for sharing this one.
You make a great point that a food industry can be contaminated and as a result cause a lot of expensive and damaging repercussions. I can imagine that if I was in charge of a food company, that I would want to be able to have a reliable way to detect when anything might fall in food like a pen or something. I am actually really interested in how people created plastic that could be detected by a metal detector.