Supercritical fluid extraction and application of bioactive ingredients from plant materials
- Like
- Digg
- Del
- Tumblr
- VKontakte
- Buffer
- Love This
- Odnoklassniki
- Meneame
- Blogger
- Amazon
- Yahoo Mail
- Gmail
- AOL
- Newsvine
- HackerNews
- Evernote
- MySpace
- Mail.ru
- Viadeo
- Line
- Comments
- Yummly
- SMS
- Viber
- Telegram
- Subscribe
- Skype
- Facebook Messenger
- Kakao
- LiveJournal
- Yammer
- Edgar
- Fintel
- Mix
- Instapaper
- Copy Link
Posted: 9 October 2016 | Nishant R Swami Hulle, R. F. Sutar, R. V. Prasad | 1 comment
Supercritical fluid extraction (SFE) technology is a green technology that offers an alternative to conventional solvent extraction technology.1 Having less impact on the environment it also meets consumer demand for safe, natural and high quality ingredients. More and more industries are using SFE technology and are reported to have market advantage.
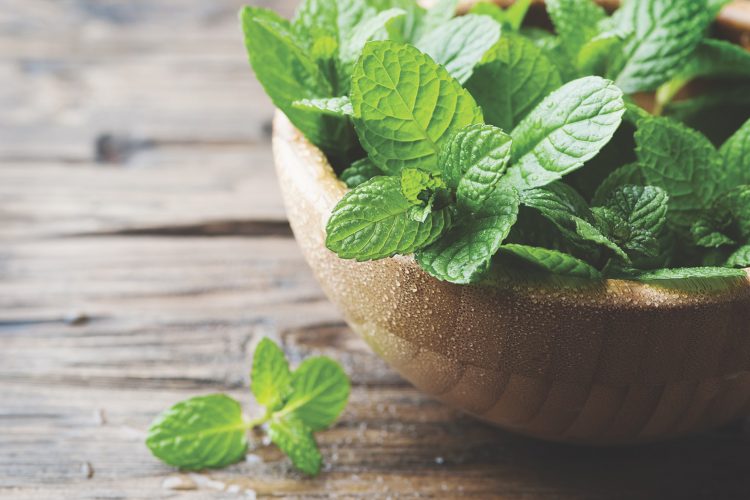
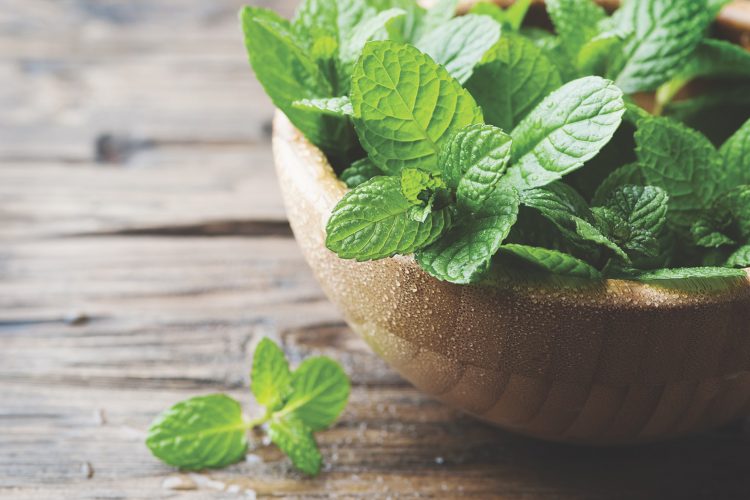
SFE is a process in which the gas beyond its critical temperature and pressure is fed to the extraction vessel in order to extract the desired compound/mixture of compounds from the product matrix (Figure 1). Under supercritical state the fluid has both the properties of gas and liquid, as it has density like liquid and viscosity like gas. This property enhances the diffusivity of the fluid in the product-containing matrix and increases the rate of extraction of the targeted compound/s. SFE is a selective process in which the process variables, such as pretreatment to plant material, temperature, pressure, particle size, moisture content, solvent flow rate, extraction time and co-solvents (usually 1 to 10 percent) are varied according to the target compound to be extracted.2
Important process variables
Pretreatment of the plant materials is an important step in preparation for SFE extraction. Pretreatment of the plant usually involves drying to reduce the moisture content and grinding for size reduction.3 As water is polar in nature it may hinder the non-polar solvent like CO2 and reduce the efficiency. Pressure and temperature are the interrelated parameters as they directly affect the solubility of the target
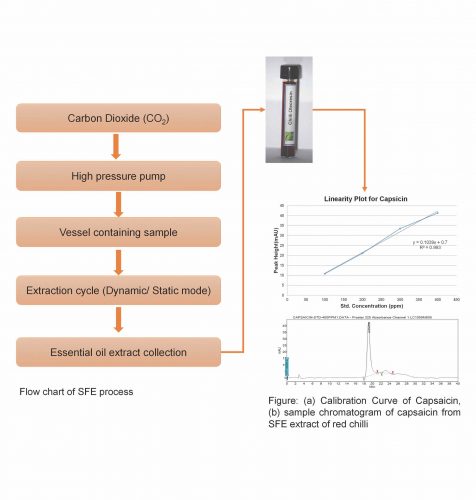
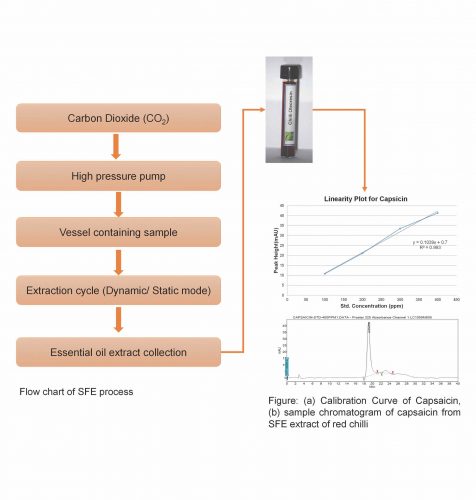
Figure 1: Typical flow chart for SFE extraction and characterisation of essential oil.
compound as well as the solvent. Solvent flow rate and extraction time are also important parameters as they directly affect the throughput of the process and economics, hence they should be carefully controlled to improve the economics of the SFE process. Grinding reduces the particle size and impermeable plant tissues, thereby increasing the surface area for its interaction with the solvent. Hence, the smaller the particle size, the greater the extraction of target compound is expected; however, too small a particle size may create a compact bed and affect the diffusion of solvent into the solid matrix. The heat generated during the fine grinding of the plant material has to be controlled in order to avoid loss of volatile compounds. The application of low temperature grinding, such as cryogenic grinding, may further improve the grinding process, which results in high quality powder. In one of the studies conducted at Anand Agricultural University (AAU) on cryogenic grinding of coriander (Coriandrum sativum L.), it was observed that during the ambient grinding the amount of volatile oil obtained was 0.133 percent whereas in the case of cryogenic grinding the amount of volatile oil content was 0.607 percent. This indicated that in the case of cryogenic grinding 22 percent more volatile oil was retained as compared to ambient grinding. Similar studies have been conducted at AAU on cumin and cardamom and process parameters have been optimised.
Due to the many process variables that affect the efficiency of the SFE extraction, systematic studies at lab scale are required for each product, which may have a different set of optimum process variables for the extraction of the target compound. There are different solvents, such as pentane, ethanol etc., that can be used in the SFE process, however, CO2 is the most widely used in industry due to its many advantages. These include a low critical pressure (72.8 bar) and temperature (30.9 °C); the fact that it’s relatively non-toxic, non-flammable, low cost and can be easily removed from the extract leaving no residue. With the recent advances in SFE technology, it is now possible to recycle the CO2 after decompression so that operational cost and emission in the atmosphere can be reduced.
Application of SFE
SFE can play a critical role in the nutraceutical and functional food industries because of its ability to extract product without solvent residue, high purity and no degradation of active compounds.4 There
Essential oils are the volatile oils obtained from the plant sources and they impart characteristic flavour and fragrance to food products. SFE has been extensively studied for extraction of essential oils from different plant sources. Some studies conducted at AAU, Anand are presented in Table 2. For example, in the case of essential oil extraction from mint, carvon was the target compound. Based on the
Apart from extraction of the bioactive compounds, SFE technology has been reportedly used for supercritical drying, coating/impregnation and particle formation which have opened up new research areas for their applications in the pharmaceutical and nutraceutical industry. Supercritical drying has been used for the drying of wet gels, while reducing the shrinkage and resulting in a superior gel matrix.
Particle design is also one of the emerging research areas where supercritical fluids are used in design and generation of particles, microspheres and microcapsules, which may find applications in pharmaceuticals and nutraceutical products. With the latest developments in SFE technology and extensive research carried out in the past, it may be concluded that this technology has enormous scope in high quality bioactives extraction from plant and other sources, to meet the current global demand of SFE extracts.
About the authors
References and further reading
- da Silva, R. P., Rocha-Santos, T. A., & Duarte, A. C. (2016). Supercritical fluid extraction of bioactive compounds.TrAC Trends in Analytical Chemistry, 76, 40-51
- Martínez, J. L. (Ed.). (2007). Supercritical fluid extraction of nutraceuticals and bioactive compounds. CRC Press
- Temelli, F., Saldaña, M. D. A., & Comin, L. (2012). Ch. 4.18 – Application of Supercritical Fluid Extraction in Food Processing A2 – Pawliszyn, Janusz Comprehensive Sampling and Sample Preparation (pp. 415-440). Oxford: Academic Press
- Pereira, C. G., & Meireles, M. A. A. (2010). Supercritical fluid extraction of bioactive compounds: fundamentals, applications and economic perspectives. Food and Bioprocess Technology, 3(3), 340-372.
The rise in the concerns of health and increase in consciousness regarding the type and source of the food and beverages is driving the global bioactive ingredients market.