5 ways that condition-based maintenance improves food safety
- Like
- Digg
- Del
- Tumblr
- VKontakte
- Buffer
- Love This
- Odnoklassniki
- Meneame
- Blogger
- Amazon
- Yahoo Mail
- Gmail
- AOL
- Newsvine
- HackerNews
- Evernote
- MySpace
- Mail.ru
- Viadeo
- Line
- Comments
- Yummly
- SMS
- Viber
- Telegram
- Subscribe
- Skype
- Facebook Messenger
- Kakao
- LiveJournal
- Yammer
- Edgar
- Fintel
- Mix
- Instapaper
- Copy Link
Posted: 3 May 2021 | New Food | No comments yet
New Food recaps the key takeaways of Infor’s most recent webinar, which highlighted the benefits of true asset performance on cost, quality, safety and sustainability.
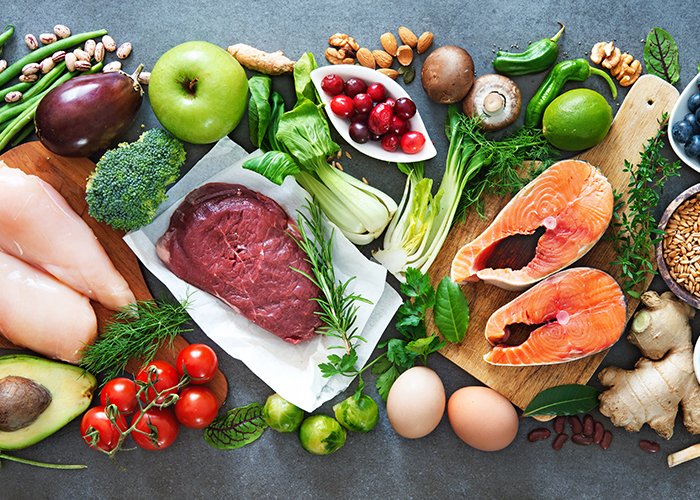
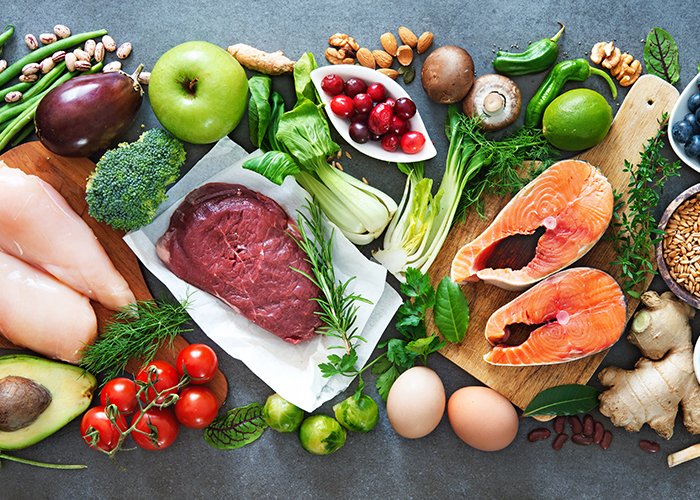
New Food recently hosted a webinar in which Nick Smalley from British Sugar and Bas Beemsterboer and Marcel Koks from Infor discussed how food and beverage producers can improve productivity and food safety by implementing Maintenance 4.0 capabilities.
Maintenance maturity of food and beverage processors
Traditionally, the maintenance function predominantly focused on keeping equipment running by fixing failures. In today’s world there is increasing pressure on food and beverage manufacturers to not only increase productivity, but also deliver safe food in a sustainable way from an environment that is safe for its workers.
Food safety problems can have many root causes. A significant number of incidents reported to the US Food and Drug Administration (FDA) and Rapid Alert System for Food and Feed (RASFF) are caused by contaminations with extraneous material, like metal pieces coming from broken equipment, grease or detergent remnants. Cross contamination and pathogens are other reasons why food and beverage manufacturers must recall products.
Many of these problems can be avoided by making maintenance an integral part of food safety procedures via the adoption of modern technologies such as the Industrial Internet of Things (IIoT), artificial intelligence (AI), and prescribing in-time service, mobility and remote service using augmented reality (AR).
Asset performance
The survey conducted during the webinar showed that many food processors are currently on the ‘Maintenance 3.0’ level. British Sugar has completed this journey successfully by using the capabilities offered by Infor EAM. This has helped to drive output, improve reliability, and ensure the safety of employees and the integrity of the products. British Sugar is now realising the factory of the future.
Mobility and remote service already show impressive benefits: technicians are a lot more productive as they can look up information and record real-time data, including photos and videos at the point of work. The technicians don’t have to repeatedly walk in and out of the clean production area – saving time and reducing contamination risks – while mobility and remote service using AR enable autonomous service by the process operators. In British Sugar’s factory of the future, IIoT sensors and AI will continuously increase asset performance in all measures.
Recording failures and data from IIoT sensors helps to understand the failure modes and criticality of assets better, so that maintenance can be more targeted. Failure mode effect analysis (FMECA) is a method to analyse what the chance of a failure is and what the consequence could be.
The five ways
True asset performance is a holistic approach that reduces costs, improves quality, ensures a safe work environment and safe food, increases asset life, and reduces waste. There are many capabilities needed to achieve this – among which, undoubtedly, people are the most important. Modern Maintenance 4.0 technology will help to achieve this via:
- IIoT sensors and real-time condition data
- AI and predictive maintenance
- Mobility
- Autonomous maintenance
- FMECA.
The transformation to Industry 4.0
The controlled environment of a company’s own manufacturing operations makes asset and equipment management a manageable starting point for Industry 4.0 experimentation in the food and beverage industry. Manufacturers that choose asset productivity as the entry point for their Industry 4.0 strategy can learn how the technologies work, revise business processes, and document best practice, which they can use to improve productivity and efficiencies within other parts of their operations.
Issue
Related topics
Data & Automation, Equipment, Processing, Robotics & automation, Technology & Innovation
Related organisations
Infor, Rapid Alert System for Food and Feed (RASFF), US Food and Drug Administration (FDA)
Related people
Bas Beemsterboer (Infor), Marcel Koks (Infor), Nick Smalley (British Sugar)