Will labour shortages break the British meat industry?
- Like
- Digg
- Del
- Tumblr
- VKontakte
- Buffer
- Love This
- Odnoklassniki
- Meneame
- Blogger
- Amazon
- Yahoo Mail
- Gmail
- AOL
- Newsvine
- HackerNews
- Evernote
- MySpace
- Mail.ru
- Viadeo
- Line
- Comments
- Yummly
- SMS
- Viber
- Telegram
- Subscribe
- Skype
- Facebook Messenger
- Kakao
- LiveJournal
- Yammer
- Edgar
- Fintel
- Mix
- Instapaper
- Copy Link
Posted: 13 August 2021 | Nan Jones | No comments yet
Nan Jones, Technical Policy Manager at the British Meat Processors Association, discusses the chronic labour shortage the meat sector is facing and asks why the situation has come to this.
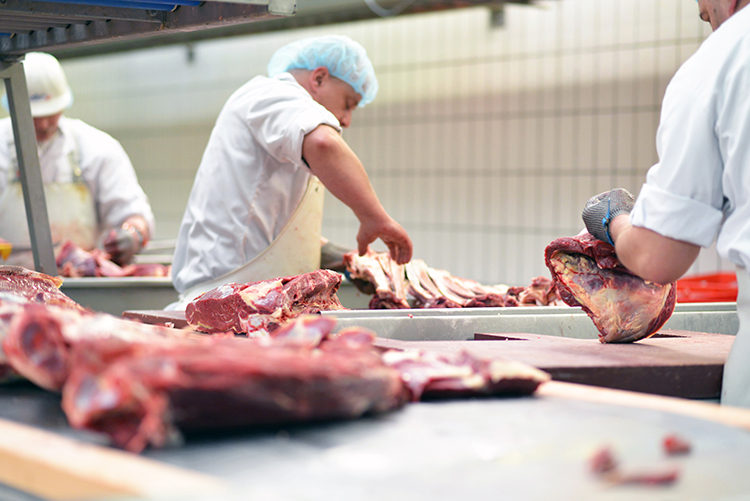
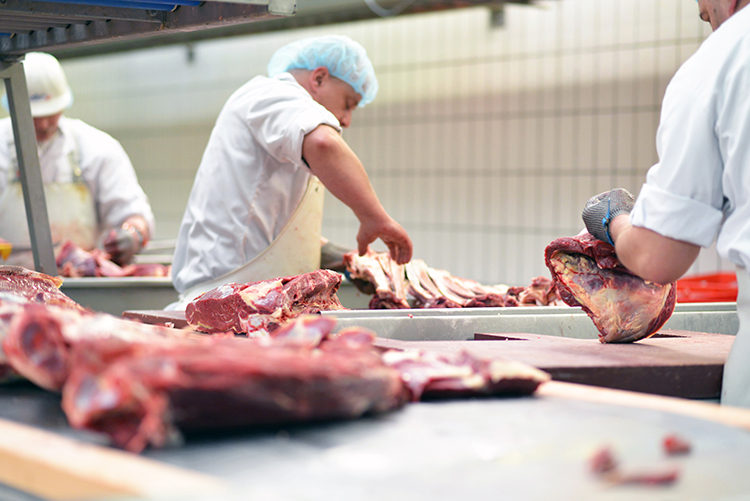
The UK meat processing industry has had a tough year so far. After dealing with heightened labour shortages from January due to Brexit, and increased absenteeism because of COVID-19, the recent test and trace ‘pingdemic’* has created a near perfect storm.
Even before the onset of COVID-19, the industry had been struggling to find employees, particularly amongst British workers, with the average shortfall over the last couple of years running at 10-11 percent. This year has seen that number rise to 15 percent, and the so-called pingdemic has added even more pain. One company last week reported a 33 percent labour shortfall at a single site. Labour and skills shortages of this magnitude could prove fatal to some meat plants if the situation is allowed to continue.
Meat processing, unlike other manufacturing, is still a very labour-intensive industry because of the level of manual dexterity needed, much of which can’t be replaced by automation. Processing plants need large numbers of skilled and semi-skilled workers to keep food production rolling, but these skills can’t be learned overnight. It takes at least 18 months to train a fully skilled butcher, so if one is lost from a production line, that person is not easily replaceable.
Once labour shortages reach around the 15 percent mark in a plant, that company is faced with some difficult decisions. Often it means they must reduce the variety of products they produce, concentrating on the simpler-to-produce but less profitable lines. Sometimes it means reducing the number of animals they take from farmers which can cause animal welfare issues. And, if enough key skilled workers are absent, it can result in the complete closure of some production lines.
Part of the labour problem stems from the fact that, for around 18 years, the meat industry has been heavily reliant on European workers to fill the labour-intensive roles. Since Brexit, many of our EU workers have returned to their home country, and access to this pool of trained migrant workers has dried up due to the new points-based immigration system. The other side of the problem is that work in the meat industry (which for a long time has not been well understood) is simply not appealing to British workers. We now also have a third angle, which is absenteeism caused by the pingdemic.
Following the chaos that the pingdemic has wrought, Government has been forced to introduce the new Daily Contact Testing scheme to try and ease pressure before the situation hits a crisis point and food shortages increase. This allows critical workers from the food supply chain who have been pinged by the NHS Covid-19 app or contacted by Test and Trace to return to work after confirming a negative Lateral Flow Test. Employees must continue to take lateral flow tests every day for seven days before entering the premises to do their shift.
The daily testing scheme is a temporary sticking plaster, but it doesn’t address the long-term labour shortage which has been getting worse for the last three years.
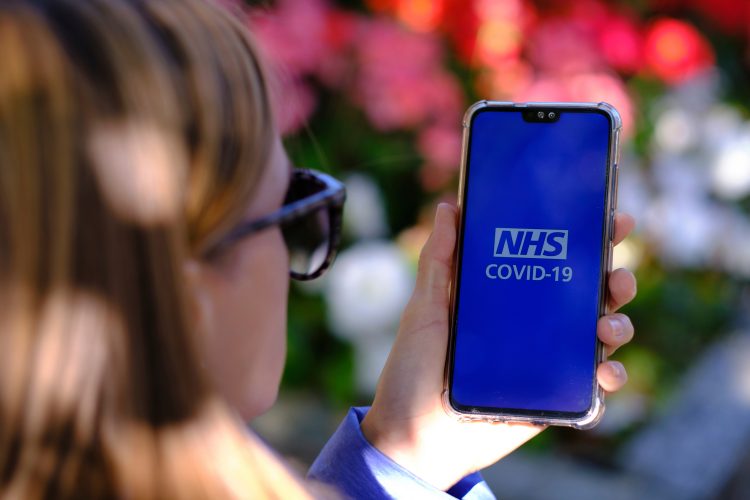
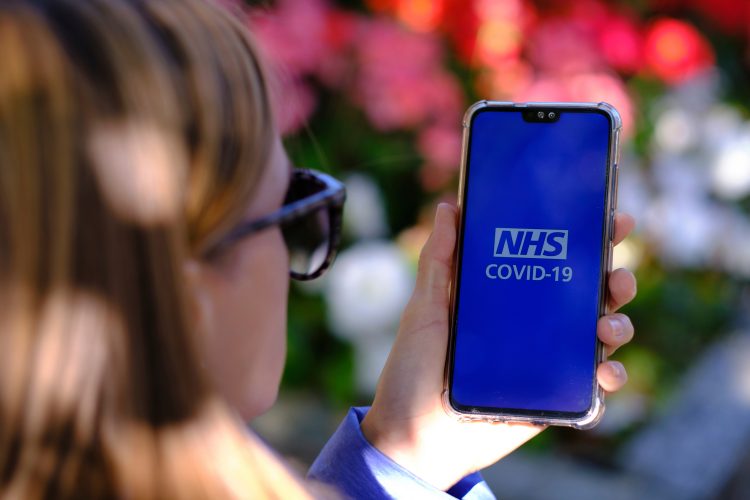
The NHS Covid app is notifying more and more people to self isolate
A finely tuned supply chain
Under normal circumstances, our ‘just-in-time’ supply chain operates as a finely-tuned machine to ensure efficient stock management of fresh, short shelf life products. Retailers have the ability to run a ‘stockless’ system, placing daily orders and reducing the risk of food waste. The sales-based ordering system allows stocks to be replenished based on daily customers’ buying patterns and it enables meat processors to produce to order.
But this fine balance has been affected by labour shortages, resulting in empty shelves in some supermarkets. This prompts panic buying among customers, which in turn triggers artificially high sales-based re-orders in the system. This puts more pressure on processors to fulfil orders but without enough staff to handle the work.
With preparations for Christmas already under way, production is even more at risk of falling behind, putting Christmas favourites like pigs in blankets at risk.
It’s now clear that there is a systemic and long-term problem with labour and skills in the British meat industry. The British Meat Processors Association along with the companies we represent have been working hard to attract new entrants to the industry, but it will take time to re-introduce the sector to job hunters who have traditionally had little exposure to the training and career opportunities it can offer.
That is why we’ve been calling on the Government for months to add butchers to the Shortage Occupation List, which would allow the industry to temporarily fill these growing vacancies with overseas workers until the current crisis has passed.
The difference now is that, if they fail to act quickly, the meat industry will hit a tipping point and British shoppers will be faced with rising prices and more empty shelves.
*Pingdemic refers to a rising number of people receiving messages from the Track and Trace app instructing them to isolate.
About the author
Nan Jones is Technical Policy Manager at the British Meat Processors Association (BMPA). She has grown up in the red meat industry, coming from a family of butchers, stretching back five generations. She graduated from Harper Adams University in Food Nutrition and Well-being and spent two years working in the technical operations team at Dunbia before joining BMPA.
Related topics
COVID-19, Recruitment & workforce, retail, Shelf life, Supply chain