What role does AI play in unlocking the food and drink sector’s £14bn growth opportunity?
- Like
- Digg
- Del
- Tumblr
- VKontakte
- Buffer
- Love This
- Odnoklassniki
- Meneame
- Blogger
- Amazon
- Yahoo Mail
- Gmail
- AOL
- Newsvine
- HackerNews
- Evernote
- MySpace
- Mail.ru
- Viadeo
- Line
- Comments
- Yummly
- SMS
- Viber
- Telegram
- Subscribe
- Skype
- Facebook Messenger
- Kakao
- LiveJournal
- Yammer
- Edgar
- Fintel
- Mix
- Instapaper
- Copy Link
Posted: 3 January 2025 | Tom Clayton | No comments yet
The food and drink industry not only has the keys to unlock £14bn in value for the UK economy but the sector could also become a world-class case study for delivering economic growth through digital innovation, believes Tom Clayton, CEO at IntelliAM.
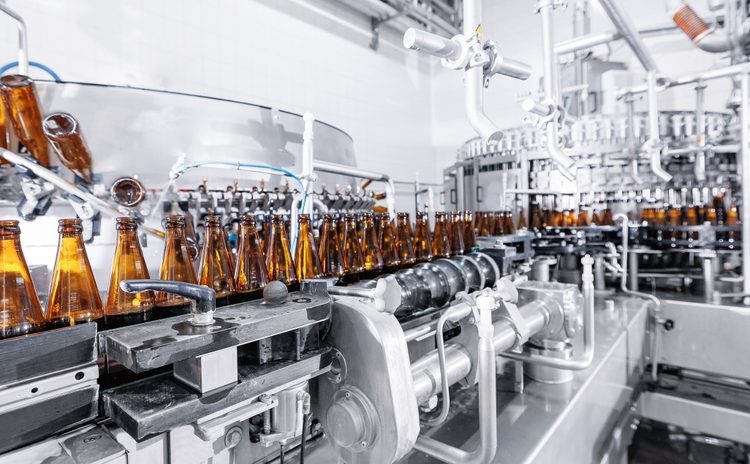
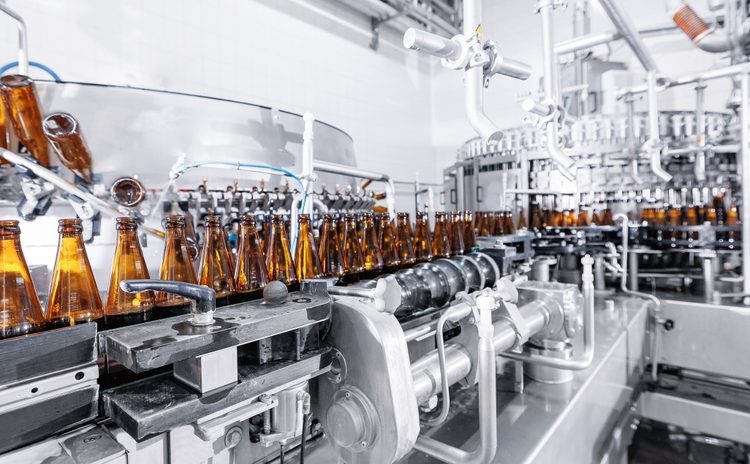
The recent report by the Food and Drink Federation, in partnership with strategic delivery consultancy Newton, certainly provided food for thought.
The Future Factory: Supercharging digital innovation in food and drink manufacturing report concluded that digital transformation in our sector is being held back by perceived risks.
I was alarmed but unsurprised to learn that 75 percent of food and drink business leaders see the benefits of digital technologies yet are reluctant to adopt them – citing fears over an immediate return, lack of qualified staff to drive transformation and a mistaken belief that legacy equipment must be replaced with expensive new kit or technology.
It is clear that the sector’s leaders think the mountain is too high to climb. But what if these so-called obstacles are more a figment of the sector’s imagination than insurmountable real-world obstacles? Mental blockers rather than physical impediments? Furthermore, what if waiting anxiously turns out to be the biggest risk of all?
At IntelliAM, we are delivering asset management services to five of the world’s top ten food and drink manufacturers. By deploying machine learning and cloud-based data analytics we are sweeping aside many of these perceived obstacles.
Contributing to the £14 billion growth opportunity identified by the Food and Drink Federation report is within our clients’ reach. These businesses are using our machine learning and AI solutions to tap into billions of manufacturing data points to improve productivity. They are not breaking the bank to rebuild factories, replace old equipment or massively upskill their shop floor. Instead, they are accessing data hidden inside their own plants and machinery.
By contextualising and layering data from existing machine PLCs, drives and IoT devices, they can improve overall equipment efficiency (OEE), increase productivity, minimise downtime and reduce energy consumption. It really is that simple.
Recently, one of our customers, a major player in the sector, implemented an OEE analysis and predictive maintenance system that harvests 400 million data points per month. Machine alarms, settings, running parameters, and product details, alongside a few additional reliability sensors to collect data – including temperature, vibration and stress wave – are all monitored.
The level of insight now afforded to them is huge. They can see when a machine is not optimally set up, access causal information on why faults occur and predict equipment failure. Since implementing this non-invasive change, line performance has increased by 10 percent.
By choosing the right reliability sensors and using parameters direct from the customers’ control equipment means no new kit, no factory floor disruption, or significant capital outlay is required.
Skilled shop floor operators and supervisors can target relevant failure modes of monitored components, whether that be vibration and temperature for induction motors or oil condition, stress waves and PLC for gear boxes.
AI and machine learning only works with manufacturing and domain expertise. But by working together, we can contextualise data including speed, pressure, product, flow and lubrication timing. Overlaying this data with reliability data allows us to monitor the health of critical components as well as vital systems such as lubrication pumps where grease levels, system pressure, and temperature can be tracked in real-time to predict potential failures and schedule maintenance proactively.
AI is revolutionising the way man and machine interact, and the beauty is that none of these pivotal changes require new factories or costly hardware and software.
The revelation in the Future Factory report that the food and drink sector is slow to unlock the power of AI and machine learning does not surprise me.
At IntelliAM, we have found that some of the biggest players in the industry are barely accessing the data that lies within their own plants. Some are accessing as little as one percent. Their digital champions are still relying on Excel spreadsheets.
The industry is ripe for overhaul and the opportunity to improve productivity is seismic. There is virtually no limit to the type of components that can be monitored whether electrical, mechanical or process based.
For those who are actively embracing intelligent asset management and the cultural shift that accompanies it, the path to transformational productivity improvement is clear. Energy reduction and improved ESG performance follow hot on the heels of enhanced productivity. The winning combination of increased productivity, reduced energy costs, improved ESG and a reliable supply of goods for a growing population demonstrates just how revolutionary AI can be.
Junaid Mujaver, a Partner at Newton, boldly states in the report: “There’s no doubt in my mind: this is the moment to harness the full power of AI, automation and digital to create a food system fit for a fast-changing world.”
We could not agree more. Every day, we see how perceived risks are being nullified. While embracing AI does require a cultural shift, careful change management processes can guide and support this transformation, making it entirely manageable.
Undoubtedly the biggest risk of all is doing nothing. A new revolution is upon us, and we must all become leaders in the science of manufacturing as technology evolves. Unlocking economic value worth £14bn and becoming truly world-class is a tantalising prospect, representing the biggest opportunity the sector has ever been granted.
About the author
Tom Clayton is the Co-Founder and Chief Executive Officer of IntelliAM. He has over 29 years of experience in the engineering industry.
Tom is a passionate advocate for AI and machine learning, believing that the answer to increased productivity can be found by tapping into billions of data points hidden within the plant and machinery of every factory in the world. He insists that machine learning solutions can be easily adopted by manufacturing. With the need to boost productivity against a backdrop of skill shortages and rising energy costs, Tom is dedicated to embedding technological convergence to transform the industry.
Related topics
Data & Automation, Equipment, Robotics & automation, Technology & Innovation, Trade & Economy