The unexpected mile: why preparation, not panic, protects lives
- Like
- Digg
- Del
- Tumblr
- VKontakte
- Buffer
- Love This
- Odnoklassniki
- Meneame
- Blogger
- Amazon
- Yahoo Mail
- Gmail
- AOL
- Newsvine
- HackerNews
- Evernote
- MySpace
- Mail.ru
- Viadeo
- Line
- Comments
- Yummly
- SMS
- Viber
- Telegram
- Subscribe
- Skype
- Facebook Messenger
- Kakao
- LiveJournal
- Yammer
- Edgar
- Fintel
- Mix
- Instapaper
- Copy Link
Posted: 14 April 2025 | Dr Darin Detwiler | No comments yet
When Dr. Darin Detwiler signed up for a 5K, he wasn’t chasing fitness goals—he was training his mindset to endure what we rarely see coming: the unexpected mile. In this deeply personal guest column, Distinguished Global Fellow in Food System Integrity Dr. Detwiler explores why true readiness is built long before crisis hits, and why the stakes are too high to leave preparation to chance.
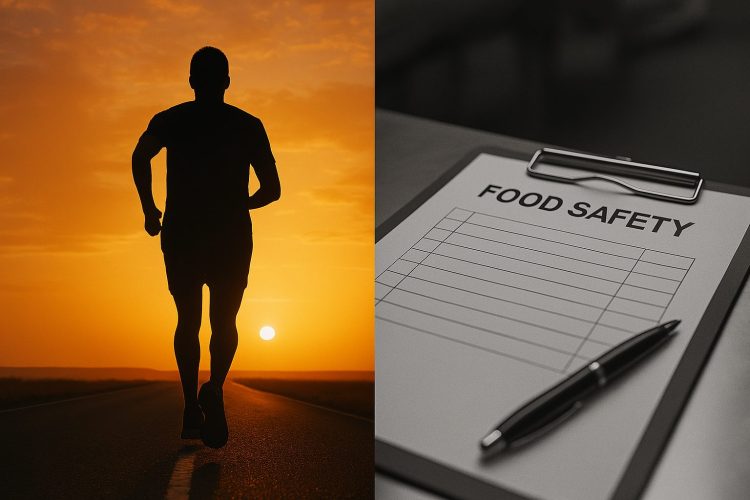
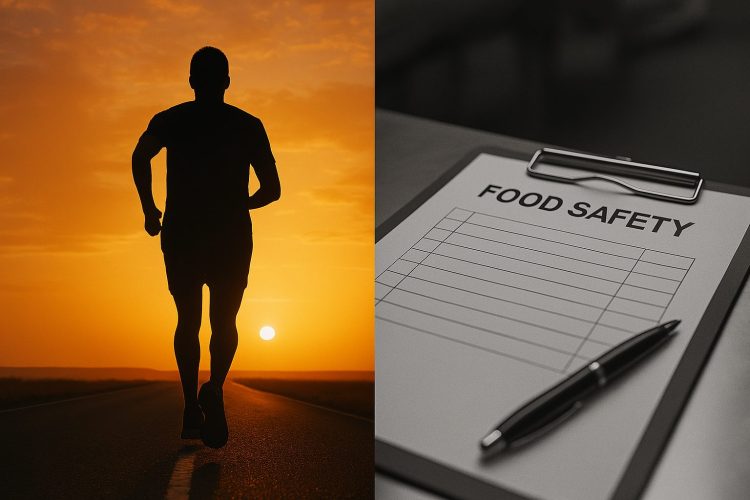
At 56, I signed up for my first five-kilometre race. Not because I love running – I don’t – but because I needed proof that real, lasting, difficult change was still possible. Over several months, I lost weight, changed my diet and walked hundreds of thousands of steps towards a healthier version of myself. But the most significant transformation wasn’t physical; it was mental.
Confidence isn’t built in chaos; it’s built in rehearsal.
Somewhere along the way, I realised this race wasn’t just about the finish line. It was about preparing for something far harder to predict: the unexpected mile. This is the stretch you didn’t anticipate: the steep incline, the brutal headwind, the moment your legs seize or your confidence falters. But the idea of the ‘unexpected mile’ reaches beyond fitness. It shows up in life, in leadership and, too often, in crises.
Anticipate and get ready
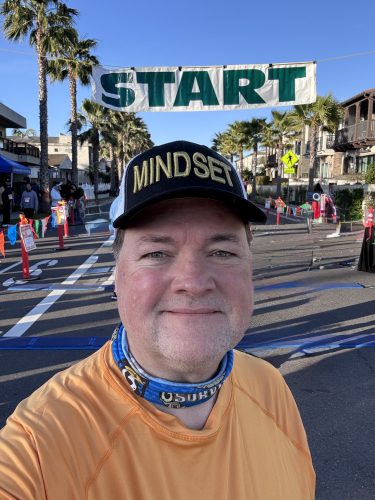
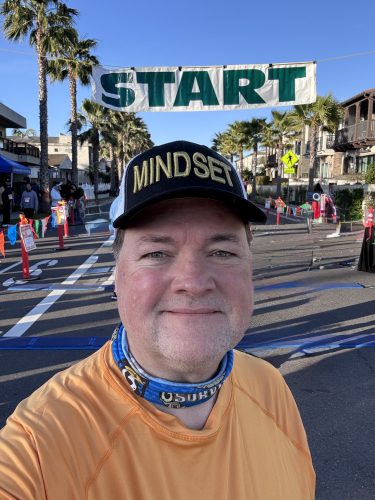
After completing his first 5K, Dr. Darin Detwiler reflects on the discipline and mindset that mirror the demands of food safety: preparation, resilience, and showing up before the crisis.
In the food industry, the unexpected mile isn’t just a supply chain disruption or a mislabelled ingredient. It’s the product recall you hoped would never come; the late-night call from regulatory authorities; the moment a single misstep – a missed test, a faulty label, a weak link in traceability – threatens lives, shatters trust and decides whether your company can respond in time.
What I’ve learnt is this: confidence isn’t built in chaos; it’s built in rehearsal.
For weeks before race day, I walked the route, studied the terrain and practiced my pace. When the pressure hit, I wasn’t relying on hope; I was relying on preparation. That discipline – the decision to show up ahead of the crisis – made all the difference.
We must prepare for those who can’t
But here’s the deeper truth: I had months to prepare for a voluntary challenge.
When my 16-month-old son Riley became sick from E. coli, my family had no time to prepare. Not for the illness; not for the horrific downward spiral that followed; and certainly not for his death, just four weeks after his first symptoms.
No time to prepare for his funeral.
No time to prepare for the grief that would gut our family.
No time to prepare for his chair, forever empty at our table.
No time to prepare for the life I’d have to build afterwards –
as a father who outlived his child, as a witness to the seemingly endless cycle of food safety failure and reform.
In the three decades since Riley’s death, I’ve met countless families who have experienced this same heartbreaking pattern. Their shock and grief are often intensified by the mistaken belief that someone – some company, some leader, some system – was working to prevent this. While my work began in the US, the patterns I’ve seen – in regulatory gaps, corporate complacency and public risk – are not unique to one country. These are global challenges.
You don’t prepare because you expect failure. You prepare because you respect the stakes.
Earlier this year, a grieving parent said something I’ve heard far too often – nearly identical to what I expressed to a reporter in 1993, standing outside a children’s hospital with my son’s window just a few stories above:
“How is this still happening – today?”
It’s not just a question. It’s an indictment: of complacency, of failed oversight, of the illusion that progress is inevitable. Behind that one sentence is disbelief, rage, sorrow and the sense that no one should have to lose a child to something preventable.
They assumed the food industry was ready for the worst-case scenario. That someone was rehearsing for the unexpected mile.
Too often, no one was.
The imperative of resilience testing
That’s why proactive preparation matters – in all its forms. Whether it’s a mock recall, a traceability audit, a supplier risk assessment, or scenario-based team training; these aren’t just box-ticking exercises for compliance, they are tests of leadership. They reveal how decisions are made under pressure, how teams communicate, how responsibilities are shared, and how ethical clarity is maintained when time is short. These tools don’t just evaluate your systems, they challenge your people to act with purpose before the crisis begins.
I once consulted with a small business trying to recover from a food safety crisis. The owners had dismissed mock recalls as unnecessary – they were busy, understaffed and confident they could manage if something went wrong. But when a mislabelled allergen slipped through their supplier, the consequences were immediate. Dozens of children became ill and the brand’s reputation unravelled overnight.
That crisis was their unexpected mile and they faced it completely unprepared
They are not alone. Across the industry, many companies – from small local producers to national brands – find themselves in the same position: overconfident, under-resourced and unready for a crisis they hope will never happen.
And this comes at a time when, across many countries, food safety systems are under strain. Public health infrastructure is stretched thin; skilled professionals are leaving the field; and trade volatility and inflation are driving companies to source from new, often less-vetted suppliers. Consumers – especially vulnerable groups – are increasingly exposed to risk.
You don’t prepare because you expect failure. You prepare because you respect the stakes.
In this perfect storm of weakened oversight, shifting economics and rising complexity, the odds of something dangerous slipping through the net are only increasing. And this isn’t just a big business problem. Risk doesn’t scale with company size – it scales with exposure. One skipped verification or a missed alert is all it takes. I’ve met too many families who thought it could never happen to them.
Make a start
So, if you’re unsure where to begin, start small but start deliberately. Take one product and walk through its lifecycle. Map one process, end to end. Review a recent food safety incident – whether it was your own or another company’s – and consider what could have been done differently. Audit your internal communication flow. Stress-test your supplier data. Time how long it takes to confirm traceability or respond to a consumer complaint.
Then, raise the complexity. Add real-world pressure: supply chain disruptions, staffing shortages, time constraints. Involve more departments – not just food safety, but procurement, marketing, executive leadership and more.
Preparation isn’t a one-time drill; it’s a mindset, a discipline, a culture of asking hard questions before the crisis hits.
And through that discipline, you don’t just prevent harm; you build confidence, resilience, and an organisation capable of protecting what matters most – before lives are on the line.
You don’t prepare because you expect failure. You prepare because you respect the stakes.
Today’s food safety leaders require the same attributes that Hercules possessed; rather than brute strength, they need strategy, adaptability and resolve. Because in the real world, the unexpected mile might be a silent supplier failure; a delayed certificate of analysis; or a breaking headline that your team wasn’t ready for.
Preparation doesn’t guarantee ease – it guarantees readiness. And sometimes, readiness is the only thing that carries you through the unexpected mile.
I finished my race. I crossed the finish line and received a small medal – not for placing, but for showing up and finishing. That medal stood for discipline, transformation and something we too often overlook: the quiet courage of preparation.
Ironically, I later found out I placed fifth in my age group. I earned a trophy I didn’t expect. But that wasn’t the point. The victory wasn’t the reward – it was the process, the mindset, the muscle memory that reminded me that I could adapt, improve and endure.
In food safety, there are no awards. No headlines for the outbreak that didn’t happen; no applause for the employee who double-checked the allergen label; and no ovation for the manager who caught a gap in supplier documentation.
Leadership means responsibility, not recognition.
It requires courage to prepare for what might never happen, and the discipline to manifest safety, trust and resilience before a crisis ever begins. If we do this together – if we build a culture that values preparation, that honours the quiet, consistent work of prevention – then we won’t just be reacting to the next crisis.
Instead, we’ll be ready for it, and we might even stop it before it ever begins.
New Food Key takeaways for food industry leaders:
- Preparation is protection: Proactive crisis planning builds trust and resilience before an incident occurs.
- Mock recalls and audits are essential: Treat them not as checkboxes, but as leadership exercises under pressure.
- Risk doesn’t scale with company size: Even small producers must stress-test traceability and supplier relationships.
- Food safety culture matters: A culture of accountability, communication and discipline can prevent the preventable.
- No one prepares alone: True food safety is a shared responsibility—from leadership to front-line staff to suppliers.
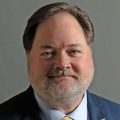
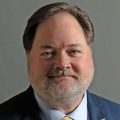
Dr. Darin Detwiler is an internationally respected food safety advocate, author, and advisor who has influenced policy and industry practices across North America and globally for over 30 years. He has served as a regulatory and consumer advisor to U.S. and Canadian federal agencies, public health authorities, and multinational food companies, shaping the landscape of food policy, education, and safety standards.
Dr. Detwiler is the author of Food Safety: Past, Present, and Predictions and a frequent keynote speaker at industry conferences and international forums. His expertise and advocacy have earned him multiple awards from the International Association for Food Protection, and he is widely recognized among the most influential figures in modern food safety. He appears in the Emmy Award–winning Netflix documentary Poisoned: The Dirty Truth About Your Food, which continues to drive global discourse around food system reform.
Related topics
Food Safety, Food Security, Outbreaks & product recalls, Supply chain