Hygienic assembly and transfer of food products: A demonstration system for the automatic processing of vegetables
- Like
- Digg
- Del
- Tumblr
- VKontakte
- Buffer
- Love This
- Odnoklassniki
- Meneame
- Blogger
- Amazon
- Yahoo Mail
- Gmail
- AOL
- Newsvine
- HackerNews
- Evernote
- MySpace
- Mail.ru
- Viadeo
- Line
- Comments
- Yummly
- SMS
- Viber
- Telegram
- Subscribe
- Skype
- Facebook Messenger
- Kakao
- LiveJournal
- Yammer
- Edgar
- Fintel
- Mix
- Instapaper
- Copy Link
Posted: 4 November 2010 | Anders Pettersson, SlK and John O. Gray, IIT | No comments yet
Food production constitutes the largest European manufacturing sector, employing some four million people and generating an annual turnover of approximately EUR 850 billion of which EUR 50 billion products are exported. The sector is unusual in that a large percentage of its output still depends on manual operations; a situation that is probably due to the way the industry has evolved over previous decades and the fact that a vast number of companies in the sector are SMEs where the take up of automation has been relatively slow throughout the European arena.
Food production constitutes the largest European manufacturing sector, employing some four million people and generating an annual turnover of approximately EUR 850 billion of which EUR 50 billion products are exported. The sector is unusual in that a large percentage of its output still depends on manual operations; a situation that is probably due to the way the industry has evolved over previous decades and the fact that a vast number of companies in the sector are SMEs where the take up of automation has been relatively slow throughout the European arena.
Food production constitutes the largest European manufacturing sector, employing some four million people and generating an annual turnover of approximately EUR 850 billion of which EUR 50 billion products are exported. The sector is unusual in that a large percentage of its output still depends on manual operations; a situation that is probably due to the way the industry has evolved over previous decades and the fact that a vast number of companies in the sector are SMEs where the take up of automation has been relatively slow throughout the European arena.
However, in the last five years, there has been a trend within the sector to adopt modern manufacturing techniques with the intro – duction of robotic and automatic procedures. Drivers include the requirements for product consistency and traceability, hygiene, waste and water minimisation, food chain security, employment legislation and, of course, ‘bottom line’ (fiscal) improvement. Europe has a vibrant automation industry but there are barriers to transferring solutions from, for example, the automobile industry to food manufacturing. Food products are generally irregular in shape, are often soft and fragile and produced in variable orientation. There is a requirement for hygienic system design (not just wash-down capability) and production runs can be quite short, requiring flexibility in automatic procedures. In this paper, we focus on the design of a production line for the automatic sorting of fruit and vegetables, and highlight how some of the challenges outlined can be addressed, with particular focus on novel gripper design and innovative visual robotic addressing orientation problems. The conclusions drawn that can benefit the design of large production facilities can be linked to novel food processing procedures.
Automatic product assembly and transfer
Once raw materials for manufacture have been hygienically processed, final products often require some form of assembly such as ‘ready meals’ and insertion in primary packaging. These procedures are traditionally accomplished manually as it is often claimed that the dexterity and flexibility of human operation is essential. Programmable robotic and automatic systems can clearly provide a high degree of functionality and flexibility, but traditional robotic grippers are generally inappropriate for the acquisition and transfer of food products, making it necessary to develop a novel set of grippers for the food sector. Ideally, such grippers should not only be designed on sound hygienic principles but also able to deal with multiple products on the same line without time consuming and complex tool changing operations.
To address this issue, novel grippers have been developed, the first prototype1 is based on the so-called Bernoulli effect. These lift objects without contact, making them particularly interesting for food products. However, the inherent drawback of this type of gripper is that it is only able to handle flat or planar products. To overcome this limitation, a deformable surface was developed. A matrix of metal pins covered with a thin rubber sheet creates a surface that can be deformed and locked (Figure 1). By gently pressing the gripper over the product (planar or 3D) and activating a set of locking bars, the gripper surface is locked into the shape of the product’s top surface. This forming enables generation of a necessary narrow space between the product and the gripper, and thus a lift force can be generated. The prototype has been shown to be able to handle a range of product shapes and variations. However, the lift force generated was limited and the grip technique is mainly suitable for smaller products with a mass of less than 70 grams.
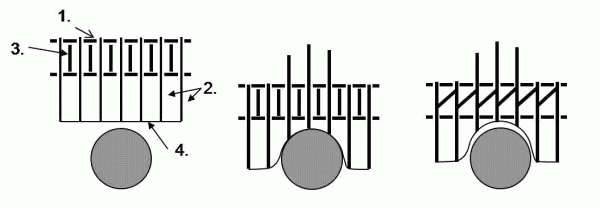
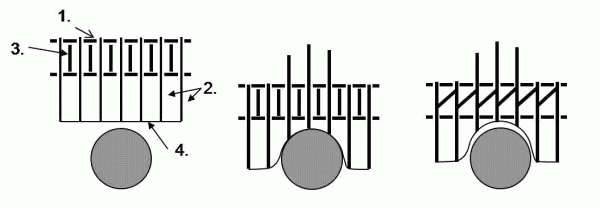
Figure 1 Schematic description of the 3D Bernoulli gripper during a shaping sequence. 1: support plates; 2: matrice pins; 3: vertical locking bars; 4: gripper surface
A combination of the Bernoulli gripper and another novel processing technique has been investigated within NovelQ. Cold plasma is a relatively new decontamination process with promising features. By replacing the air flow used in a Bernoulli gripper with cold plasma, decontamination and handling could be achieved in a single step. Furthermore, as the Bernoulli gripper does not make contact during the lifting, the entire product can be treated with cold plasma, avoiding shadowed spots. Initial results using this combination have been negative, but an explanation and solution may be possible1.
A second prototype2 was developed that utilises phase-shifting properties of a Magneto rheological (MR) fluid. On each arm of the parallel arm gripper, an electromagnet was attached and a pouch of MR-fluid bonded to the surface (Figure 2). In ambient conditions, an MR fluid behaves akin to motor oil with low viscous flow. However, a magnetic field induces a phase-shift; the fluid becomes a semi-solid with a pronounced yield stress and a consistency likened to peanut butter or toothpaste. During gripping, the pouches of MR-fluid are pressed against the sides of the product and softly deforms around its contours, exerting very little force. As the gripper arms reach a standstill, the electromagnets are activated and the MR-fluid solidifies, geometrically locking the product into a perfect mould. This gripper has shown promising results: it is able to handle a range of products including apples, tomatoes, straw – berries, broccoli and grapes, and exerts extremely low forces during handling.
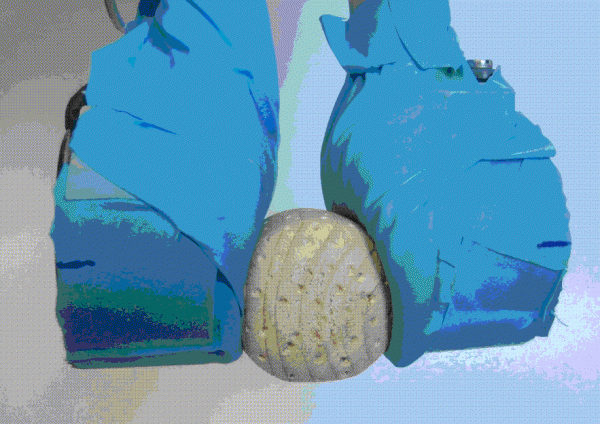
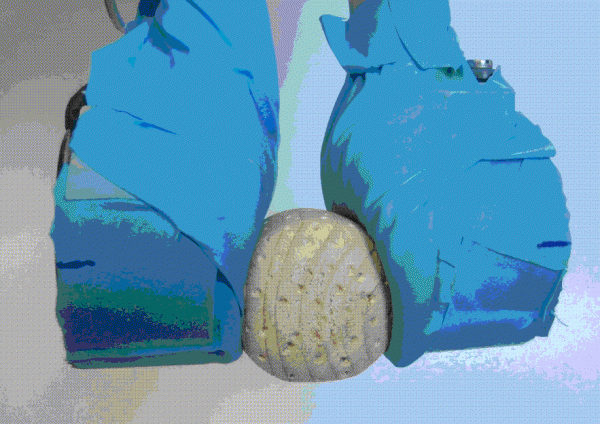
Figure 2 MR-fluid gripper arms holding a wooden model of a strawberry
One difficulty encountered with the MR-fluid gripper is making a design suitable for washing down with a hose. The linear motion of the gripper arms is difficult to seal against ingress of microorganisms and / or moisture into the mechanism. A third prototype has been developed to address this problem, and to demonstrate an alternative approach for delicate gripping. This gripper uses a parallel arm actuator but it is equipped with a force sensor, enabling slim gripper arms and delicate grip forming, and a magnetic coupling. The magnetic coupling is used to enable encapsulation of the complete drive unit in a box (Figure 3). With a magnetic coupling, the force moving the gripper arm can be transferred through the box wall. A set of magnets is fastened on the linear mechanism inside the box and a corresponding set of magnets on the gripper arm. This concept allows for a completely hygienic, washable gripper to be designed.
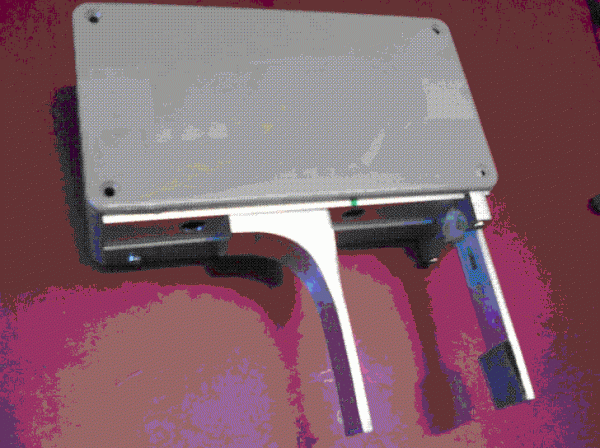
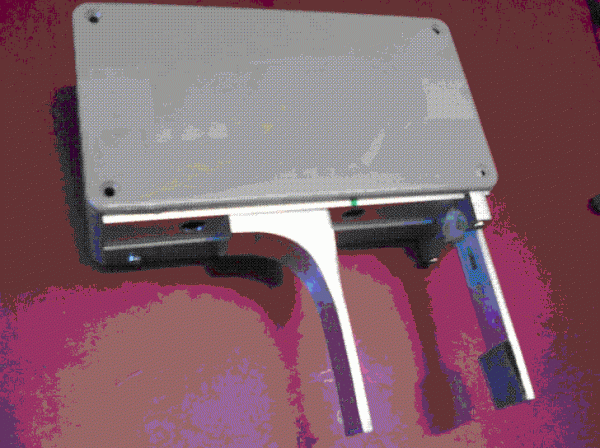
Figure 3 Enclosed parallel arm gripper actuator with force sensor and magnetic coupling. The base of the moving arm (left) contains the set of magnets
This prototype has demonstrated the concept is valid: with the force gripper and the data extracted from the vision system, each product type can be gripped with a specific set grip force (Figure 4). Although the design allows for hygienic handling, additional decontamination during handling may be beneficial, and a potential automated de contamination process has been tested with promising results. Products with a grip width of 5 – 65 millimetres and a weight of approximately 0 – 500 grams can be handled including apples, tomatoes, strawberries, carrots, grapes and broccoli3. Further development will include stainless steel casing, which can be hosed down, increased grip force and reduced grip time.


Figure 4 Presentation of grip force and grip time graphs for various grip force settings
A demonstration system for the handling of vegetables
A complete demonstrator has been developed to better understand and demonstrate the potential offered by a flexible, hygienic handling system for fragile food products (Figure 5). In a cleanroom facility at SIK (SE), a robot equipped with the new flexible force gripper has been installed to demonstrate flexible handling and production with fragile food products prior to primary packing.
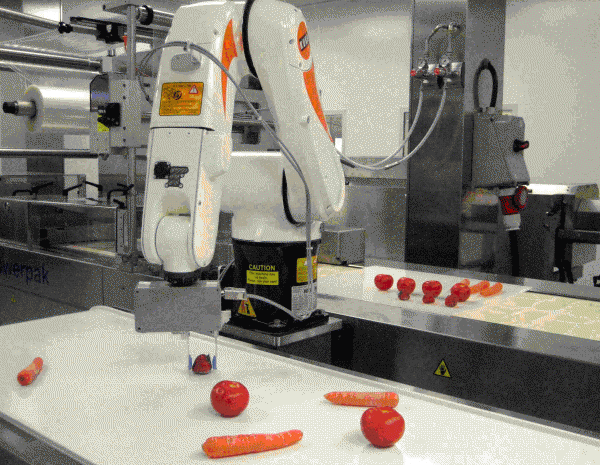
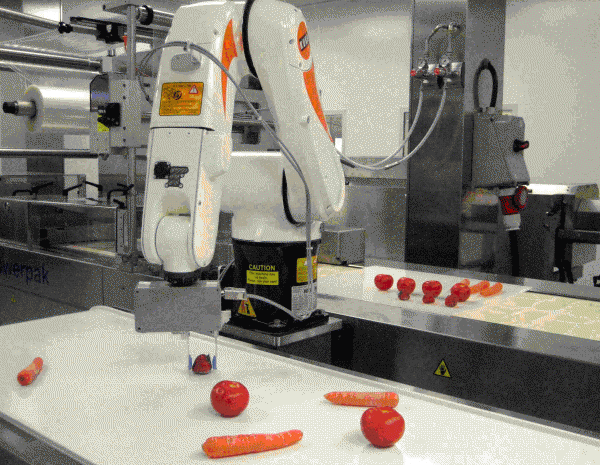
Figure 5 Robot station during flexible production. Variable and fragile products arrive mixed to the robot and are individually handled and placed according to the layout designed in the GUI
An IP68 encapsulated vision system has been programmed to distinguish between apples, tomatoes, carrots, small carrots, strawberries, broccoli and grapes. This enables individual grip forces, and thus a strawberry can be handled using as little force between the gripper arms as 50 grams whilst higher forces are used for harder products such as carrots.
To make full use of the flexibility provided by a robot, it is very important to be able to re-program it. As this traditionally requires specialist skills, not always available in a food plant, steps towards more intuitive re-programming have been investigated. Instead of traditional robot programming, a graphical user interface (GUI) approach was tested (Figure 6). Products can be selected by a button click. An image of the product appears that can be dragged, dropped and rotated freely by the operator using a PC mouse. Multiple products can be selected to form the desired product layout. When a satisfactory layout has been designed, production is started by pressing a button.
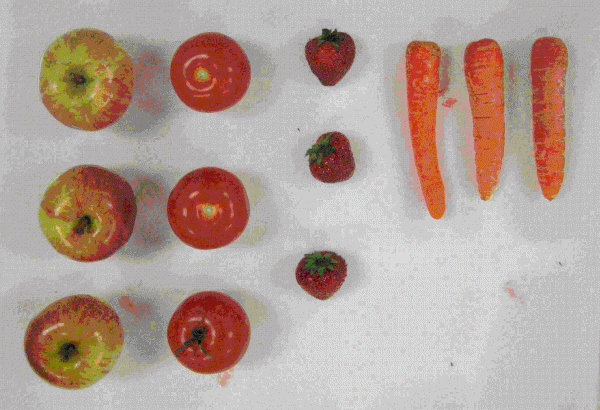
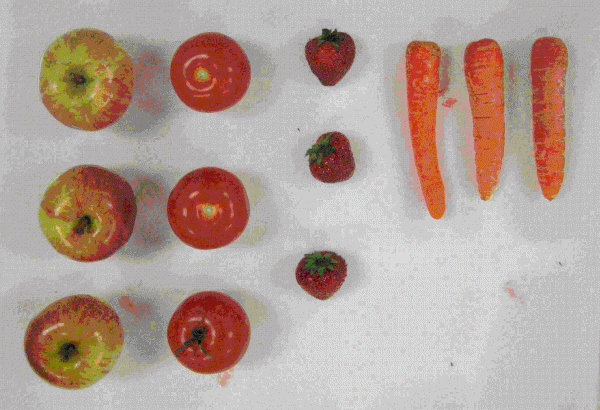
- Figure 6 Resulting production after completely automated robot handling with a flexible gripper
The products are identified and parameters extracted by the vision system as they arrive to the robot. Each product is matched against the product layout, as defined in the GUI. Product matches are sent to the robot and queued until the product is within reach of the robot. For each product, grip force and gripper separation is set from vision data as the gripper is moved into position by the robot (Figure 5). A grip command is initiated by the robot and the gripper grips the product to a spe
cified individual grip force suitable for that product type. The product is placed at the coordinates corresponding to the layout in the GUI (Figure 7).
Figure 7 Graphical User Interface (GUI) for product placement planning using drag and drop
The demonstrator shows the concept of a flexible robotic production unit for fragile and variable food products, and a new product layout can easily be redesigned using the GUI. If the right products are supplied, the changeover time is zero. No aligners are needed as the robot and vision system can cope with random placement and orientation. A continuous and mixed inflow of products can be processed by one single robot station with each product transferred individually to avoid bruising or denting.
Conclusions and future work
Hygienic manufacturing encompasses the entire operation from the input of raw ingredients to the processing and packaging of the final product. A significant improvement in hygiene can be accomplished by removing, as far as possible, human operators from physical contact with food products and replacing their function with fully automated procedures. Such procedures can be designed to be inherently hygienic in all operational, procedural and maintenance matters, and can be further exploited by use of containment concepts, which enable manufacturing in – for example – inert or UV-radiated environments. Recent advances in robotic technology and noncontact sensing has made ideal manufacturing scenarios possible, although there is still significant work to be undertaken to develop ‘off-the-shelf’ solutions tailored to food industry needs. From a fairly slow start in 2000, recently there has been rapid uptake of automation technology within the sector and it is one of the fastest growing markets for robotic application in the UK, for example. The driver is not just hygienic operation although this is vital but other strong economic factors that impact directly on the sustainability, efficiency and profitability of the industry.
Acknowledgement
This study has been carried out with financial support from the Commission of the European Communities, Framework 6, Priority 5 ‘Food Quality and Safety’, Integrated Project NovelQ FP6-CT-2006-015710.
References
1. Pettersson, J. A., Ohlsson, T., Dodd, T. J., Gray, J. O., Davis, S., & Caldwell, D. G. (2010). A Bernoulli Principle Gripper for Handling of Planar and 3 Dimensional (Food) Products, Submitted to Industrial Robot, accepted 2010-07-13
2. Pettersson, A., Davis, S., Gray, J. O., Dodd, T. J., & Ohlsson, T. (2010). Design of a magnetorheological robot gripper for handling of delicate food products with varying shapes. Journal of Food Engineering, Vol. 98, iss. 3, pp. 332-338
3. Pettersson, A., Ohlsson, T., Davis., Gray, J. O., & Dodd, T. J. (2010). A hygienically designed force gripper for flexible handling of variable and easily damaged natural food products. Submitted 2010
About the Author
Anders Pettersson
With a background as a food material scientist at SIK and with a recent MSc degree in mechatronics, Anders has tried to approach this project from both a food science and from an engineering point of view. The project has furthermore formed the core of Anders’ doctoral studies which has been performed in connection to the University of Sheffield.