The need to adapt
- Like
- Digg
- Del
- Tumblr
- VKontakte
- Buffer
- Love This
- Odnoklassniki
- Meneame
- Blogger
- Amazon
- Yahoo Mail
- Gmail
- AOL
- Newsvine
- HackerNews
- Evernote
- MySpace
- Mail.ru
- Viadeo
- Line
- Comments
- Yummly
- SMS
- Viber
- Telegram
- Subscribe
- Skype
- Facebook Messenger
- Kakao
- LiveJournal
- Yammer
- Edgar
- Fintel
- Mix
- Instapaper
- Copy Link
Posted: 15 December 2010 | Toyota Material Handling Europe | No comments yet
Forklift trucks have been the established method for moving and storing goods in the food and beverage industry for decades, and while the basic concept of a unit load conveyed by two forks has largely remained constant, the types of truck employed have evolved in the quest for improved use of space and maximum productivity at the lowest cost.
Forklift trucks have been the established method for moving and storing goods in the food and beverage industry for decades, and while the basic concept of a unit load conveyed by two forks has largely remained constant, the types of truck employed have evolved in the quest for improved use of space and maximum productivity at the lowest cost.
Forklift trucks have been the established method for moving and storing goods in the food and beverage industry for decades, and while the basic concept of a unit load conveyed by two forks has largely remained constant, the types of truck employed have evolved in the quest for improved use of space and maximum productivity at the lowest cost.
As a result, the materials handling industry has developed a wide range of products to suit differing needs, whether it be loading/ unloading, transportation, movement of goods in manufacturing, order picking or straight – forward storage. The maturity of the industry has resulted in clear synergies between manufacturers, with most companies responding to typical customer demands by offering broadly the same types of trucks – albeit with varying performance, features and benefits. However, despite the choices on offer for many truck users, there remains a need to adapt.
Toyota Material Handling Europe (TMHE) has a long history of working closely with customers to adapt trucks to match precise requirements. Dedicated facilities within TMHE’s production units are able to interpret customer needs and design optimal solutions. There are generally four main reasons that drive the need to adapt.
Adapting to the working environment
There are many examples in which the working environment demands change to a standard truck. Food manufacturing requires the highest standards of hygiene, and trucks can be built of stainless steel, allowing regular washing and resisting corrosion. In contrast, milling environments demand adaptation to protect equipment against the ingress of dust.
“We do of course find that many customers have similar requirements,” explains Niclas Sternerup, Vice President, Special Products, in Mjölby, Sweden, “and we have the ability to use some designs in many different applications, which is of course a significant cost benefit. For more mainstream special environments like cold stores we have suitably engineered trucks as part of our standard offer. But we recognise that there are always going to be more unique customer situations that we need to respond to.”
However, other less obvious environmental issues can also call for the need to adapt. The daily goods industry often involves round-the-clock operation, and night deliveries in residential areas. So TMHE has developed trucks for silent operation – an excellent example of working with customers to solve operational problems. Designed to comply with the PEAK programme in the Netherlands (www.piek.org), the ‘Silent’ BT Levio LWE200 is modified to be as quiet as possible in ‘on-vehicle’ applications making evening and early morning deliveries in residential areas.
The standard LWE200 is modified in several respects. Tolerances on moving parts such as the lift system and the castor wheel linkage are tightened. Damping materials are added to certain parts of the chassis and forks to reduce vibration. Sound damping material is also added under the covers. The overall effect isto bring noise levels from the truck down to 60 dBA in use. But it is not just the work environment that can demand the need to adapt.
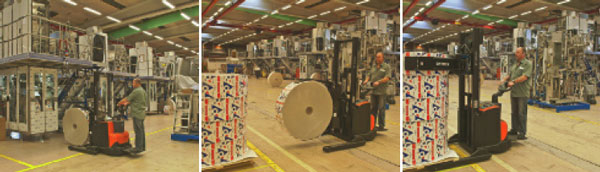
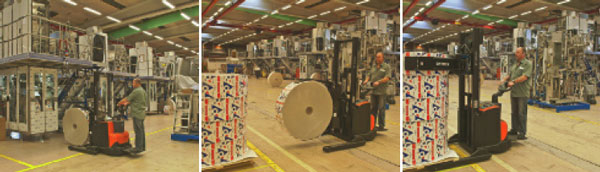
The BT Staxio SWE120 is fitted with a rotating clamp to handle rolls of unfilled drinks cartons. These are taken horizontally from stacks, rotated vertical and loaded into dairy machines that produce filled containers.
Adapting to the load
In some food and beverage operations adaptation can be required to deal with the type of load being handled. The concept of a unit load – usually palletised – is well established, allowing handling by most conventional types of truck. However in some applications the load may have different characteristics.
Less stable consignments may require additional support to ensure safe and efficient handling. This could involve specially designed stability aids, with for example overhead support to steady the load from above, or a lateral tilt facility to ‘nest’ the load. A frequent example of this is high-stacked roll cages of products such as dairy cartons, which demand high and fast throughput without risk of spillage.
An example of a truck modified to support the load from above can be found at one Swedish dairy company. Their BT Stratos LRE160L machines from Toyota Material Handling are modified in two respects. Firstly, as they operate in a chilled environment, they are fitted with a complete cab, including heating system. For load handling, they have a clamping system mounted to the fork carriage that allows them to safely handle pallets of stacked milk containers that are not shrink-wrapped, and would, therefore, be impossible to handle securely on a standard truck. The truck operator can lower the clamp with a lever inside the cab.
In other cases the load is not palletised at all, instead using side clamps, which can be an effective way of lifting large unit loads such as domestic appliances. Likewise lifting devices may be a better option to aid the driver in lifting heavy loads that would normally be handled by two people.
Adapting to the process
While materials handling equipment is principally employed in the storage and distribution industry, there are also requirements in situations where straightforward lifting and lowering of a load is insufficient.
In food and beverage manufacturing, forklift trucks can be adapted to fulfil a variety of tasks. The process may require a tool, component or raw material to be fed or loaded in a way that could involve rotation, inversion or other manipulation. This type of adaptation is also within the scope of TMHE’s special product development units.
BT Staxio SWE120 powered stackers, modified with rotating clamps, are in wide – spread use by a well known Swedish drinks packaging manufacturer. These are designed to handle large rolls of ‘flat’ cartons, taking them from horizontal stacks on pallets to load themvertically into dairy machines that produce filled containers. The operator is in full control of the clamping force. Part of this company’s standard specification is a manometer mounted into the truck body to show the clamp pressure, allowing the operator to judge the right amount of pressure needed to handle the load securely but without damaging it.
Streamlining the process
Improvements in logistics may in some cases be calculated in fractions of cents, but the consequential commercial impact measured in multi-digit units of currency. A slight adjustment to the way something is handled may only appear to gain a few seconds, but when that process is repeated many times per hour, per shift, per week and per year the time savings can be impressive, impacting on both manpower and equipment costs.
This is the other reason why progressive companies often choose to adapt trucks to precisely suit the needs of their operations. For example, an adapted workspace within the cab of a truck can streamline a process, ensuring that the tools and equipment required to support the flow of an operation are in the right place at the right time.
TMHE’s Special Products division also makes many modifications to bring standard trucks into line with local or customer regulations. Examples include the fitting of seat belts with sensors preventing a truck from being driven if the belt is not fastened, and the fitting of overhead guards to stand-in low-lifters that operate in high-racking areas.
Efficiency in materials handling is essential in any business, and in some cases it can have a substantial impact on profitability. The industry has been seeking innovation in handling for decades, and most mainstream requirements can be satisfied with the wide ranges of trucks that manufacturers offer today. But for many companies there remains the need for tailoring.
The number of customer-adapted solutions developed by TMHE illustrates the point. “With over seven thousand different versions of trucks currently available, our biggest challenge is sharing our experience with our customers,” continues Sternerup. “While we will always be able to design and build to order there is a wealth of ideas and experience within our existing library of adaptations.”
For more information about Toyota Material Handling Europe’s products and services, visit www.toyota-forklifts.eu
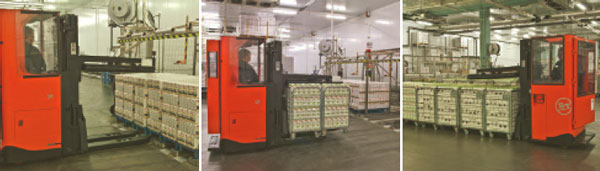
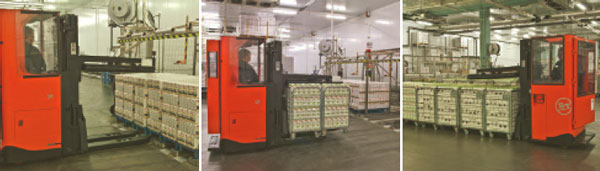
The BT Stratos SRE160L is fitted with a clamping system that allows it to securely handle mini pallets of stacked drinks containers that are not shrink-wrapped. The same truck is used to handle similar products in mini rollcages.