Are you prepared for the implications of FSMA regulations?
- Like
- Digg
- Del
- Tumblr
- VKontakte
- Buffer
- Love This
- Odnoklassniki
- Meneame
- Blogger
- Amazon
- Yahoo Mail
- Gmail
- AOL
- Newsvine
- HackerNews
- Evernote
- MySpace
- Mail.ru
- Viadeo
- Line
- Comments
- Yummly
- SMS
- Viber
- Telegram
- Subscribe
- Skype
- Facebook Messenger
- Kakao
- LiveJournal
- Yammer
- Edgar
- Fintel
- Mix
- Instapaper
- Copy Link
Posted: 2 May 2017 | Michael Koeris | CEO | Sample6 | No comments yet
Exclusive insight from CEO Sample6 Michael Koeris on how to ensure your EMP is ready for the FSMA regulation.
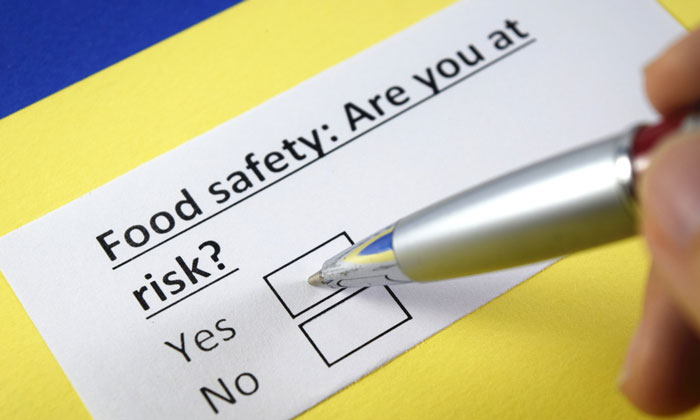
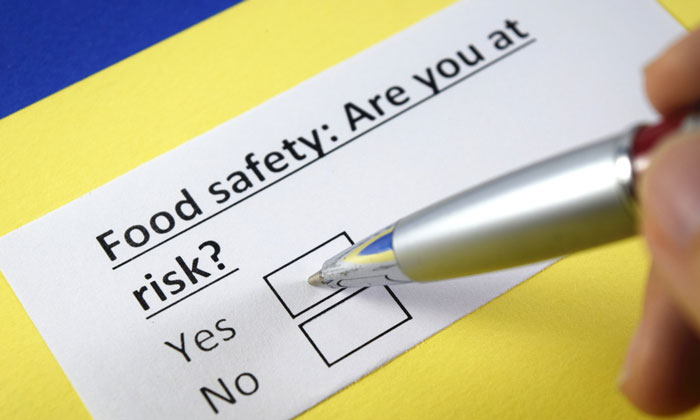
As the Food Safety Modernisation Act (FSMA) compliance deadlines loom the manufacturing industry is preparing for the full rollout. By September 2017, every plant with more than a few million dollars in revenue must ensure that its environmental monitoring program (EMP) has adapted to this unprecedented shift. While some plants may think that their EMP is ready to meet these compliance demands, the unfortunate reality is that many of them are not.
If you haven’t applied the proper adjustments to your company’s plan for monitoring, testing, documentation and risk assessment, you may be facing noncompliance. Now is the time to find out if your facility is on track. The responsibility to implement a proactive food safety approach is greater than ever, and it’s vital to identify any areas in which your EMP may not be sufficient. To get a clearer picture of where your manufacturing company stands in terms of FSMA compliance, consider these critical questions:
Where does your list of sampling points exist?
Think about your current process for keeping track of environmental sampling points. Are you manually recording them in a spreadsheet or, worse, relying on a paper trail? These options may have served you well in the past, but today’s food safety requirements necessitate a more modern approach. Unless you’ve adopted an electronic management system (EMS) that keeps your sampling points digitally organised in one easily accessible and highly visible location, you carry an unduly risk for errors in execution or compliance and that puts your customers and brand at risk!
While some plants may think that their EMP is ready to meet these compliance demands, the unfortunate reality is that many of them are not…
With a high-quality EMS in place, you have the ability to view your plant in its entirety and see every test point at whichever level of detail is required. By implementing this next-generation solution to sample data management, you can reduce time, effort and inaccuracy — all of which are essential to fulfilling the stringent contamination prevention standards of FSMA.
How well does your entire food safety & quality team know these sampling points?
If you can’t positively say that every member of your Food Safety, Quality and Sanitation team knows these environmental sampling points, you have work to do.
The strength of the team’s visibility in this area impacts their accountability for carrying out an EMP that’s ready to meet FSMA requirements. From determining sample order and testing schedules to ensuring proper zone coverage, it is crucial for each individual to have sampling point information at their fingertips.
Can you easily track compliance with the sampling plan (e.g., timing, quantity, locations)?
Your environmental sampling plan is only as good as your ability to track every aspect of it, from department to department, all across the plant. This is an intricate, complex endeavour requiring reliable, automated tracking measures. One of the reasons why this tracking is such a challenge is the volume and diversity of the data. A typical EMP is testing 10-15 samples per week per line, and many are 3-4 times that – just for pathogen detection, not to mention higher multiples for routine sanitation and pre-op testing.
To fully satisfy FSMA regulations, your plant is tasked with identifying areas of weakness in the production process that may lead to contamination or other safety issues, and then enforcing controls to minimise or eliminate those risks. To achieve the kind of visibility needed to pinpoint these areas of weakness and overcome them, you must place a major focus on data, particularly with regard to your environmental sampling plan. It’s important to employ an EMP software package that equips your team with valuable access to robust sampling data for tracking purposes.
Only a well-structured EMP supported by innovative food safety software makes achieving a high level of tracking and coordination a reality. With easy access to an organized database of policies, workflows and reporting, you have a sound method of ensuring compliance.
How is an alert – either a positive result or out-of-spec result – triggered and communicated?
Strong communication is essential to running a successful EMP. Without it, you can’t properly and efficiently address the food safety challenges occurring throughout your facility. Your plant is a dynamic operation with many departments and functions, so you must be able to foster cross-department communication and get everyone involved in your EMP. This is especially true when it comes to relaying positive or out-of-spec results. If your current process involves triggering and communicating these alerts manually, you’re risking errors and delays that can cause more widespread contamination risks.
In preparing to meet the strict food safety standards of FSMA, your EMP should leverage a solution that enables fluent communication between departments and provides visibility to all teams and stakeholders. It should be designed to send automatic alerts and notifications that relay time-sensitive results to the right people immediately. Otherwise, you’re not in a position to proactively minimise and contain pathogen hazards.
Do you feel that corrective actions are transparent throughout your organisation?
Any effective EMP is going to see a small percentage of presumed positives. This should be expected as you tighten your monitoring program and enforce greater prevention controls. What you need in order to respond to those positives is a thorough remediation process, including the tools to track, record and communicate corrective actions.
This enables your facility to learn from a positive, use it to improve the overall condition of the environment and, therefore, improve pathogen prevention. But if corrective actions are not transparent throughout your organisation, the team is not equipped to address contamination issues appropriately and comply with FSMA mandates. So, ask yourself:
- Are you employing a solution that documents the specific tasks required by your food safety plan to re-mediate a problem?
- Can the sanitation crew easily review SOPs and attach corrective action documentation, including notes, pictures and maintenance forms?
- Can other managers and team members within the company view progress at every step of the corrective action process and view the supporting documentation?
- Is retest data instantly accessible for verifying that the corrective actions have been effective?
Environmental management software is highly valuable in properly sharing the necessary information to overcome food safety risks and ensure regulatory compliance.
For a regulatory inspection (FDA, USDA, etc.), would you be able to supply requested sampling documents within 24 hours?
From single-day to multi-day inspections, FSMA is raising the bar on food safety assessments, and this will affect your plant’s ability to keep pace. The audit preparations and practices you’ve been applying for years may no longer be sufficient for this new wave of compliance. If you end up facing an inspection, you’ll need to provide documentation for several aspects of your food safety plan, including your:
- HACCP/HARPC documentation
- SOPs
- Routine testing results
- Investigative testing results
- Corrective actions
The best way to accomplish this is by having it all digitally stored in a centralised database that can organise and produce the required materials in less than 24 hours. Documentation that’s stored and accessible in a pinch puts your operation in a better position to meet FSMA requirements.
What is your average wait time to be notified for positive results and/or failures?
With most types of environmental testing methods, food processors don’t have the ability to properly respond to positives or failures because they don’t receive the results until the next day or later. This causes corrective actions to lag the incident by 24-48 hours. In this amount of time, a “hot spot” can migrate due to foot traffic, product flow or other factors in the normal course of producing food. If your average wait time is excessive, you end up pushing quality and safety to the back end of your process, and putting hours worth of production at risk.
This is no way to operate – and it certainly isn’t an effective or efficient means of meeting the many food safety changes and compliance requirements challenging your plant. That’s why it’s important to secure a testing solution that breaks through this data-lag barrier and provides results within six hours, from sample to response.
This fast data feeds your EMP, allowing you to test all surface areas for enhanced coverage and reduction of risk. You’re able to address and contain test positives in the most efficient way possible. You can make food processing, shipping and sanitation decisions much more quickly, as well as enforce preventive controls much more promptly. This is one of the best ways to prepare your EMP for FSMA compliance.
Don’t put your organisation at risk of noncompliance. Make sure that your EMP is ready for the evolved safety demands posed by the rollout of FSMA. To see if your environmental monitoring program is as prepared as it needs to be, take this free FSMA Assessment quiz.