Current trends in spray drying research: Understanding the development of particle stickiness enables controlling agglomeration during dehydration
- Like
- Digg
- Del
- Tumblr
- VKontakte
- Buffer
- Love This
- Odnoklassniki
- Meneame
- Blogger
- Amazon
- Yahoo Mail
- Gmail
- AOL
- Newsvine
- HackerNews
- Evernote
- MySpace
- Mail.ru
- Viadeo
- Line
- Comments
- Yummly
- SMS
- Viber
- Telegram
- Subscribe
- Skype
- Facebook Messenger
- Kakao
- LiveJournal
- Yammer
- Edgar
- Fintel
- Mix
- Instapaper
- Copy Link
Posted: 7 July 2011 | Alessandro Gianfrancesco & Stefan Palzer, Nestle | 1 comment
Spray drying is a widely used technique to produce a broad range of industrial powders. For instance, within Nestle, the largest product volumes such as powdered infant formulas (e.g. NAN®) and pure soluble coffee (Nescafe®) are manufactured through spray drying. The goal for manufacturers of such powders is to make sure that the obtained particles have a good mechanical stability to avoid breakage during transportation, that the powder has the right density for packaging and dosage purposes and that the products rehydrate easily for final consumption (favourable ‘instant’ properties).
However, particles produced by simple spray drying can be smaller than 50μm in diameter, leading to poor flowability and slow reconstitution or lump formation during rehydration. Thus, usually a further agglomera – tion step is required to increase the particle size and to modify the particle structure in order to improve the final quality of the powder.
Spray drying is a widely used technique to produce a broad range of industrial powders. For instance, within Nestle, the largest product volumes such as powdered infant formulas (e.g. NAN®) and pure soluble coffee (Nescafe®) are manufactured through spray drying. The goal for manufacturers of such powders is to make sure that the obtained particles have a good mechanical stability to avoid breakage during transportation, that the powder has the right density for packaging and dosage purposes and that the products rehydrate easily for final consumption (favourable ‘instant’ properties). However, particles produced by simple spray drying can be smaller than 50μm in diameter, leading to poor flowability and slow reconstitution or lump formation during rehydration. Thus, usually a further agglomera - tion step is required to increase the particle size and to modify the particle structure in order to improve the final quality of the powder.
Spray drying is a widely used technique to produce a broad range of industrial powders. For instance, within Nestle, the largest product volumes such as powdered infant formulas (e.g. NAN®) and pure soluble coffee (Nescafe®) are manufactured through spray drying. The goal for manufacturers of such powders is to make sure that the obtained particles have a good mechanical stability to avoid breakage during transportation, that the powder has the right density for packaging and dosage purposes and that the products rehydrate easily for final consumption (favourable ‘instant’ properties).
However, particles produced by simple spray drying can be smaller than 50μm in diameter, leading to poor flowability and slow reconstitution or lump formation during rehydration. Thus, usually a further agglomera – tion step is required to increase the particle size and to modify the particle structure in order to improve the final quality of the powder.
In industrial spray drying practices, powder agglomeration can be performed by either retaining fines by integrated filter bags inside the dryer or re-circulating fines which have been separated from the exhaust air. These fine particles are separated from the exhaust air stream by using cyclones or bag filters. They can be added back into fluid beds installed in- or outside the drying chamber or just blown back into the main drying chamber or added to the generated droplets close to the atomiser. All these possibilities can also be combined. The particle growth and the structure of agglomerates obtained depend on several factors such as collision probability, (which is a function of particle /drop density), the force and direction/geometry of the impact and the surface properties of the colliding particles.
One of the biggest challenges with existing spray drying systems is controlling the fines insertion location in order to adjust the agglomeration degree to the desired extent in any specific operating condition and for every considered recipe.
Particle agglomeration during spray drying
Agglomeration requires collisions between two or more particles, followed by adhesion. At the moment of the impact, at least one collision partner must have an adhesive surface in order to form stable bridges between particles.
The stickiness of amorphous particles can be related to their glass transition temperature Tg. A particle becomes adhesive / sticky when its surface reaches a critical viscosity value of 106 – 108 Pa∙s. A material whose viscosity lies in this range is said to be in the rubbery state. Such viscosity is given at temperatures which are more then 10-30°C higher than the glass transition temperature Tg of the material. Accordingly, the so-called sticky temperature Tsticky is 10 to 30 degrees above Tg. Significantly above Tsticky, particles can be considered as more or less viscous liquid drops, while below Tg their surface is no longer sticky and thus a stable dry powder is obtained. The glass transition temperature of a material depends on water content and water activity of the considered product (Tg = f(aw)), which changes quickly during drying. Thus, a particle’s stickiness can be directly related to the drying kinetics.
Depending on the physical state of the particles’ surface, several kinds of collisions are possible inside a spray drying chamber:
- Collisions between two liquid drops. This leads to coalescence, resulting in the formation of a slightly bigger droplet but no porous agglomerate is obtained
- Collisions between a liquid drop and a dry particle. In this case, a nonporous onion structure is formed, in which the solid dry particle is covered by the liquid (coating)
- Collisions between two dry particles (below Tg). No adhesion occurs, and particles tend to rebound after the impact
- Collisions between a dry and a sticky particle. For instance, if dry fine particles are returned inside the chamber, they may collide with drying particles. This type of collision results in the formation of semi-liquid bridges that are further dried leading to stable solid bridges. Fast re-hydrating agglomerates with a grape-like structure might be obtained
The force of the collision (direction, kinetic energy) may also influence the structure (porosity) of the formed agglomerates and the stability of the established bridges between adhering particles. The kinetic energy transformed upon collision into deformation depends on the particles’ relative speed and mass (pressure at collision).
In order to produce mechanically stable instant powders, it is desirable to obtain particle structures between the compact and the loose grape structure, with medium porosity. In order to obtain the desired structures, one must control the agglomeration process during spray-drying. For this purpose, the evolution of particles properties (temperature and water content at surface) during drying should be monitored, in order to identify the regions inside the drying chamber where particles are sticky. Thus would enable design processes that favour collisions between sticky particles.
Measuring the evolution of particle properties during drying
In current industrial practices, spray drying is considered as a ‘black box’ in which only the inlet and outlet air properties are controlled. To characterise a product’s evolution during drying, one option involves direct powder sampling inside the chamber. However, several drawbacks are associated with this measure – ment technique, such as the long sampling time needed and the evolution of sample properties during the collection itself. This technique is also invasive and not easily applicable to all types of spray dryers.
Due to the fast water evaporation from liquid drops, the air temperature and relative humidity also evolve inside the chamber, and their evolution is representative of the drying kinetics. While air temperatures inside spray dryers have been measured by several authors, few studies report about measurements of air relative humidity inside the chamber. This has never been investigated at the industrial scale. Such a measurement coupled with air temperature allows one to determine the air absolute humidity Y (kg water/kg dry air) at different positions inside the dryer. Then the mass balance for water in the air between the air inlet and the measuring point can be established. The amount of water evaporated at several positions inside the chamber can be calculated, and thus the product’s average water content can be determined numerically.
The evolution of powder/particle temp – erature is also defined by the air’s properties. At the beginning, while drops are still liquid, their temperature will be equal to wet bulb temperature of the inlet air. This temp – erature depends on the inlet airs temperature and humidity. It varies from 40 to 60°C under standard spray drying conditions.
Once most of the water has been removed, the particle’s temperature will gradually increase and eventually be in equilibrium with surrounding air. Thus, the outlet air temperature measured at the exit of the chamber can be considered as the maximum temperature for the powder.
In our research, thermocouples and hygrometers were successfully installed in a pilot-scale spray dryer, and the measurements showed the fast evaporation occurring in the upper part of the drying chamber. In the zone close to the atomiser, up to 90 per cent of water was evaporated. The product’s temperature always remained between 45 and 75°C, so that thermal degradation is avoided.
In our studies, one of the major difficulties encountered was finding the right setup and locations to install the temperature and RH probes, in order to avoid direct liquid spraying and/or powder deposition on the probes. Furthermore, in order to correctly interpret the experimental data one must know the air and particles flow pattern inside the chamber. This can be obtained through numerical simulation.
Numerical simulation of air flow pattern and particle trajectories
Commercial Computational Fluid Dynamics (CFD) software (e.g. Fluent®) can be used to predict air and particle trajectories as well as the evolution of particle moisture and temperature during spray drying. Some attention should be paid to the definition of the right computational grid size and the definition of the turbulence model to be applied. Due to the high computational time, 2D simulations at steady state would be preferred.
Thanks to the simulation, it is possible to visualise air backflow zones, and to study the influence of the chamber design on the air flow and particles’ trajectories.
Commercial software is not adapted to calculate the drying behaviour of materials as complex as food products. Several research projects are currently focusing on the development of specific drying models for real products which could be integrated into CFD codes. As an example, the completed EDECAD project (www.edecad.com) aimed at combining CFD simulations of spray drying with particle surface properties at the moment of collision to simulate agglomeration inside the chamber.
Determination of sticky zones in a pilot spray dryer
Knowing the evolution of temperature and average water content of the drop/particle, it is possible to illustrate the drying pattern of a solution droplet in a temperature / wateractivity (aw) or water content diagram in which the sticky regions are highlighted (Figure 1). The water activity at the particles surface is linked to the particles water content by a sorption isotherm. Depending on the product’s material properties (glass transition curve, sorption isotherms), stickiness will occur within a certain water content range and thus in specific regions in the drying chamber.
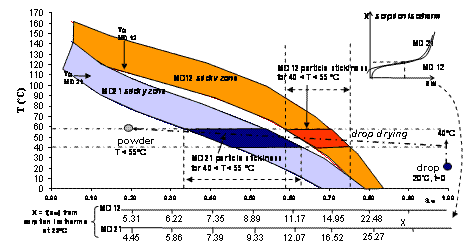
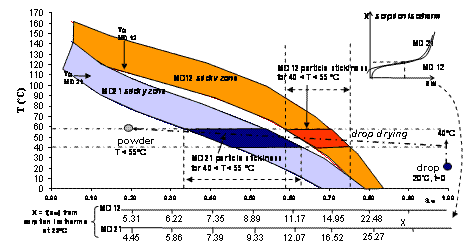
Figure 1 Evolution of particle properties and sticky zones along drying for two different materials (maltodextrin DE12 and DE21).
From the simulated particles’ trajectories, it is possible to identify zones within the dryer in which the particle surface possesses the favourable viscosity range for agglomeration. This knowledge can be used to optimise process conditions for agglomeration and/or to prevent particles from adhering to the chamber’s walls or inside the cyclone.
Controlling the degree of agglomeration during spray drying
Effective agglomeration requires collisions between two or more particles while they are in the sticky state. To some extent, this can occur spontaneously due to air turbulence inside the dryer. Nestlé’s EGRON spray dryers have an open roof, which causes an increased level of turbulence and thus enhance the probability of collisions. However, most of the agglomera – tion during spray drying is generally obtained by recycling small particles (called fines, d < 50μm) back into the chamber, in order to allow contact between the fines and drops that are still humid. In industrial practice, fines are usually added back close to the atomisation zone because here the particle density is larger and thus the probability of collision is the highest. However, this is not always the best choice for agglomeration, as recycled dry particles become covered by the liquid drops (coating), without a significant size increase and generation of porosity. The position where re-circulated fines are inserted into spray towers can thus be modified depending on the desired degree of agglomeration. When a strong size increase is required, fines can be inserted directly into the sticky zones, where they will collide with adhesive semi-dried droplets/particles. This will lead to the formation of a grape-like structure, which exhibits good reconstitution properties. On the other hand, when a higher density and higher mechanical stability of the final product is required, fines can still be reinserted close to the atomisation region.
Conclusion
The optimisation of agglomeration during spray drying leads to the production of better powders in terms of rehydration behaviour and/or mechanical stability. It is possible to modulate the agglomeration process by adjusting the position at which dry fine particle which have been separated from the exhaust air are added back inside the chamber. The choice of the appropriate location for addition of fines requires the knowledge of the zones in which particles become adhesive during drying at varying operating parameters. In our research, we demonstrated that it is possible to couple appropriate measurements of air temperature and relative humidity inside the chamber with numerical simulation of air and particle flow patterns, in order to identify sticky zones inside the dryer. This also requires the knowledge of important material properties such as glass transition temperature and its dependency on the moisture content and recipe. These findings can support the design of new fines insertion systems in order to control and further improve the agglomeration degree during the spray drying process.
About the Authors
Alessandro Gianfrancesco graduated in 2005 from the Politecnico of Milan (Italy) with an MSc in Chemical Engineering. He obtained a PhD in Food Process Engineering in 2008 from AgroParisTech (France), with a thesis on spray drying process. Alessandro is now working at the Nestle Research Center in Lausanne (Switzerland) as a research engineer, specialised in drying and powder technologies. He is also deputy leader of the Nestlé Agglomeration & Drying Expert Network.
Stefan Palzer graduated in 1996 from the Technical University of Munich (Germany) with an engineering/MSc. degree. He obtained a PhD in Process Engineering in 2000 from the same University. He joined Nestle in 2000 as product developer for dehydrated food products in Switzerland. End of 2007 he was promoted head of Food Science & Technology department at the Nestle Research Centre in Lausanne (Switzerland). In 2008, he additionally took over the responsibility for the 12 Nestle Food Science Expert Networks. In 2010, Stefan was promoted to Managing Director of Nestlé’s global research and development centre for confectionery (York, UK). Stefan is also a visiting professor for chemical engineering at the University of Sheffield and honorary professor for food science at the university of Stuttgart-Hohenheim. Stefan is the author of more than 150 scientific publica – tions and inventor of more than 20 patents.
Highly informative and useful article..