Water treatment through blending leads to better beer
- Like
- Digg
- Del
- Tumblr
- VKontakte
- Buffer
- Love This
- Odnoklassniki
- Meneame
- Blogger
- Amazon
- Yahoo Mail
- Gmail
- AOL
- Newsvine
- HackerNews
- Evernote
- MySpace
- Mail.ru
- Viadeo
- Line
- Comments
- Yummly
- SMS
- Viber
- Telegram
- Subscribe
- Skype
- Facebook Messenger
- Kakao
- LiveJournal
- Yammer
- Edgar
- Fintel
- Mix
- Instapaper
- Copy Link
Posted: 19 November 2018 | Egon Huefner | No comments yet
When it comes to beer, the better the water quality, the better the end result – which is why successful blending is so important to the process. Egon Huefner outlines the procedure at traditional Swiss brewers, Eggers.
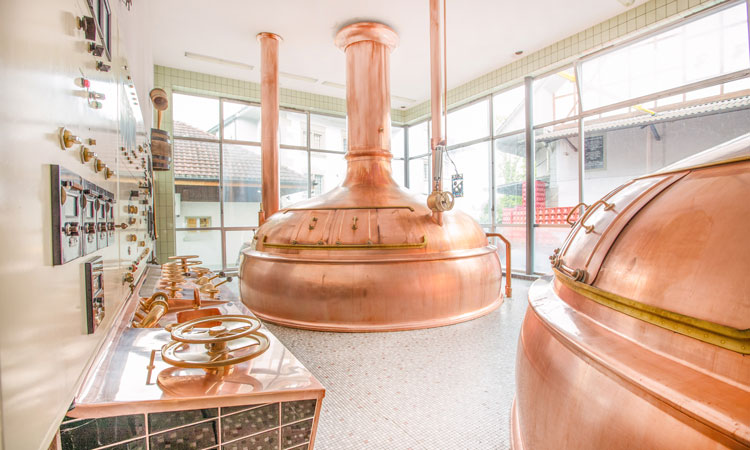
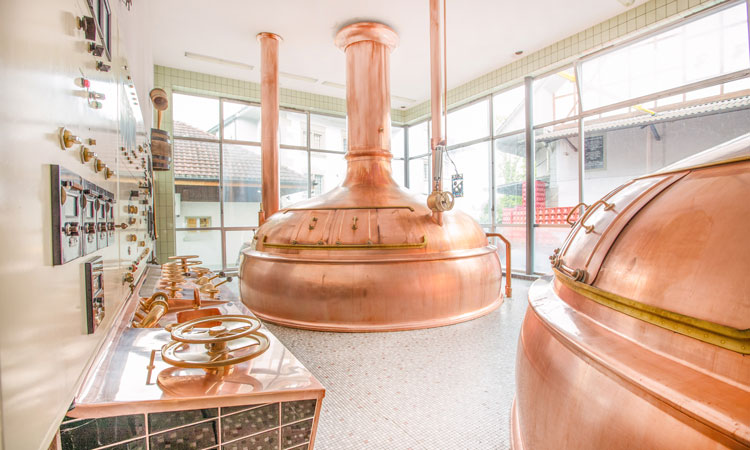
Water constitutes an essential element in the food and beverage industries. A technique that is often used entails blending raw water with processed water until the required quality is achieved, directly in the end user’s plant. Modern, stand-alone solutions are now available that use blending controllers to monitor the process, promote economical process water management and can be retrofitted without interrupting operations. This article illustrates the process for beer making.
The main purpose of blending is to produce a water mix of defined quality; eg, with a certain degree of hardness, level of conductivity, or sulphate or chloride content. Two basic techniques are used for blending: proportional regulation and qualitative regulation. In the first case, the desired result is achieved by blending raw water and treated water (eg, demineralised water) in specific proportions. This technique is only suitable if the water quality of the two water types remains constant.
In the second case, two different water qualities are combined to achieve a predefined output quality; eg, conductivity. After blending, the water quality is monitored (eg, by means of measuring conductivity) continuously and maintained by regulating the blending proportions. The type of treatment required determines which technique is best suited in any given case. This in turn depends on the industry and the application concerned.
Cooling towers and plants for ventilation technology (AC re-cooling) often necessitate that the degree of hardness, the electrical conductivity or the sulphate and chloride content be reduced. For irrigation systems in plant cultivation, the salt content is an important factor that needs to be measured to prevent substrate salinisation.
To take a specific food application: a master brewer decides on the parameters that are required to produce the right brewing water for each type of beer being brewed to ensure consistent taste. The important parameters here include the pH value, the water hardness, sulphate content and so on.
Determining the blending principle for beer
Where reverse osmosis is used to extract salts from water, the result is pure water – known as the permeate – and, because relatively few ions remain, it conducts practically no electricity. The salt content of the blended water can then be determined very accurately by means of a conductivity measurement. This represents a blending system’s control variable. If, on the other hand, an ion exchanger is used (knowing the conductivity is of no help because ions are simply ‘exchanged’), the conductivity remains almost the same. In such cases, an alternative is needed – if possible, this may be simple proportional blending.
The main purpose of blending is to produce a water mix of defined quality
To produce blended water with a particular degree of hardness, both techniques require that the raw water quality remains essentially constant. However, if the raw water hardness varies, then a combination of proportional regulation and qualitative regulation is required. Here, the raw water hardness is recorded and the blending controller calculates precisely the correct ratio of raw water to treated water; this results in exactly the right hardness of blended water. In all cases, the regulation must be carried out precisely and quickly, and even where boundary conditions change (eg, variable flow rates), the quality of the blended water must meet the requirements as closely as possible, to ensure constant production conditions.
A practical blending solution
Depending on the production process – ie, whether the raw water quality is constant or variable – modified blending principles are required to deliver the correct water quality. Therefore, the most practical solution consists of a stand-alone operation that saves the plant operator from having to intervene in existing plant processes. The main component here is the blending controller. This device may be a conductivity regulator with a conductivity sensor in the blended water, or a proportional regulator, or a regulator that takes account of other parameters, such as the hardness of the raw water, to produce the right mix. In some cases, analogue or digital interfaces may be necessary to facilitate communication with the main process control system.
The plan was to operate independently of the production control system, producing brewing water of the required quality
In order to address the many and varied requirements of water quality control, modular blending units that can deal with practically all usage scenarios that may arise are the best option. This is where the user will benefit from a broad product portfolio of components that are designed to work perfectly with each other. Depending on the flow rate, flow meters and control valves ranging from small (DN 6mm) to large diameters (DN 100mm) are available. All components, including the sensors, can be supplied in plastic, brass or stainless steel, as required.
In addition, many different sensors are available, as well as flowmeters that use magnetic-inductive principles, ultrasound or the impeller wheel principle. The control valves can be electrically- or pneumatically-driven seat valves or ball valves with electromotive actuators. This means that every plant engineer can order an individual solution that is then supplied as a fully functional unit. A tailored solution can be guaranteed for everyone: from the small-scale, manually-operated craft beer brewery to a major water treatment plant with complex process controls for a large factory.
Blending water for brewing
An example of such blending systems in use can be found in the treatment of water for the brewing industry. The taste and quality of a beer is highly dependent on the quality of the brewing water. It is no coincidence that large and small breweries alike have flourished in locations that have a natural supply of especially suitable water. These days, in order to maintain a characteristic beer taste – and meet standards of quality – breweries must use water treatment plants. The decisive parameter in such cases is the degree of hardness. Soft water is needed to allow the beer aroma to develop – a fact well known by the master brewers of the traditional Swiss Egger brewery in Worb near Bern. The company’s origins go back more than 150 years. Michael Egger, Production & GL Manager, explains: “We are fortunate in that even before we started using a water treatment plant, our well water was already very pure and of high quality. In the past, our main problem had to do with the relatively high calcium content in the raw water. This led to scale buildup, especially in parts of the plant using hot water, as well as equipment malfunctions and therefore a lot of extra maintenance work.”
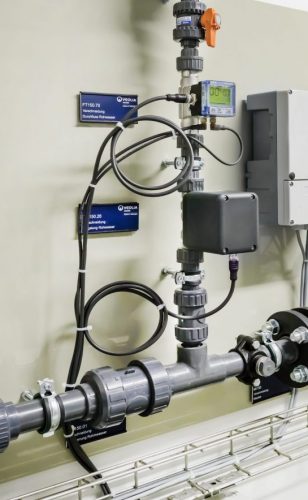
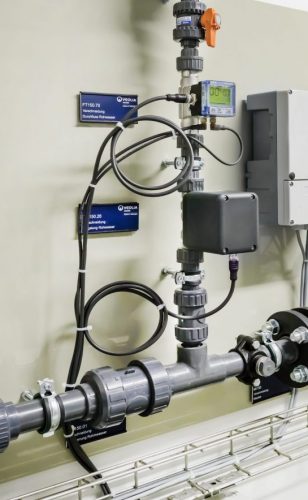
The brewery’s requirements were met by means of a stand-alone blending unit with carefully chosen components.
The task facing the plant engineering company, Veolia Water Technologies Deutschland GmbH, was to implement a tailored water treatment plant with regulated blending in the brewery as a stand-alone solution. This plant was to operate independently of the production control system, producing brewing water of the required quality, with precision and reliability, for the subsequent production processes.
These requirements were attained by means of a blending unit, which we supplied. The Veolia treatment plant splits the raw water into two separate streams: one remains untreated and one provides the infeed for the reverse osmosis process. The raw water is then fed into the salt-free permeate from the reverse osmosis process in a constant proportion, which can also be adjusted. As the quality of the raw water is stable, this fixed proportional setting suffices to meet the quality requirements. The blending proportions are controlled by means of a Type 8611 compact controller. In addition, the fast-response Type 8011 and Type S030 flow meters measure the flow rates of each stream. This produces the right blend of brewing water, reliably and with the desired quality.
Good brewing water and optimised operating costs
The blending system ensures that no more permeate is used than is necessary. This saves money in the reverse osmosis process and means longer maintenance intervals for the plant, which also has a longer lifespan. As a result, the Egger brewery not only increased the quality of its products, but also improved its cost effectiveness. “The new system means significantly less outlay for cleaning, descaling, maintenance and repairs. In addition, the energy consumption is lower because the heat transfer performance of the plate heat exchangers has improved,” adds Michael Egger.
As the plant also operates on a batch basis – in other words, it periodically replenishes a tank that is used to supply the continuous production of beer – it was also possible to install the system without interrupting the production process. As a consequence, there is now a supply of water for brewing whose quality remains constant. This in turn ensures that each recipe delivers a consistent taste for the type of beer concerned; and all achieved without modifying the existing plant.
Issue
Related topics
Equipment, Health & Nutrition, Ingredients, Processing, Quality analysis & quality control (QA/QC), The consumer
Related organisations
Burkert Fluid Control Systems, Egger brewery, Veolia Water Technologies Deutschland GmbH