Predicting the future of maintenance
- Like
- Digg
- Del
- Tumblr
- VKontakte
- Buffer
- Love This
- Odnoklassniki
- Meneame
- Blogger
- Amazon
- Yahoo Mail
- Gmail
- AOL
- Newsvine
- HackerNews
- Evernote
- MySpace
- Mail.ru
- Viadeo
- Line
- Comments
- Yummly
- SMS
- Viber
- Telegram
- Subscribe
- Skype
- Facebook Messenger
- Kakao
- LiveJournal
- Yammer
- Edgar
- Fintel
- Mix
- Instapaper
- Copy Link
Posted: 21 August 2019 | Darcy Simonis - Industry Network Leader for ABB’s Food and Beverage | 1 comment
While uncertainty around Brexit continues to dominate headlines, one thing that is clear is the impact that the loss of skilled overseas workers will have on the UK engineering industry. Darcy Simonis, Industry Network Leader for ABB’s Food and Beverage segment, explains the future of maintenance in the food and beverage industry.
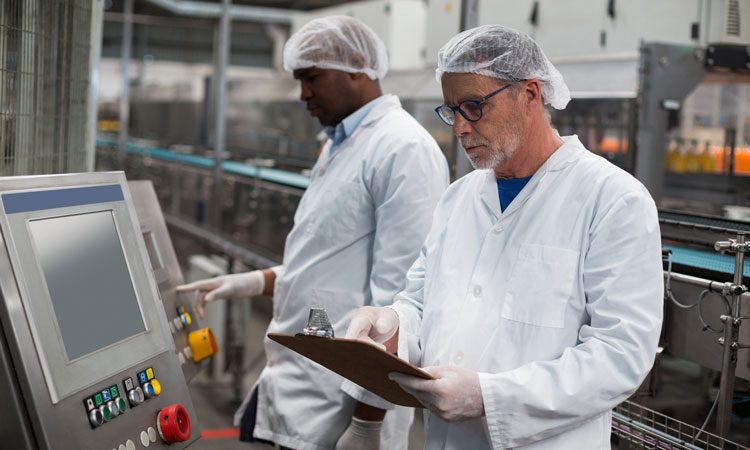
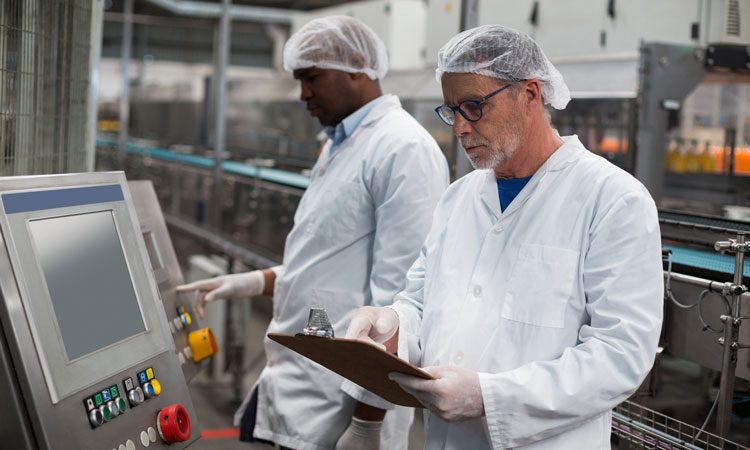
In 2018, EngineeringUK estimated that by 2024 there will be an engineering skills deficit of over 265,000 workers. With this in mind, plant managers are being advised to plan for the loss of technical expertise and knowledge.
Manpower Groups’ 2018 talent survey shows that skilled traders and technicians are in the top five hardest roles to fill in the global economy. Losing such a large percentage of skilled workers is problematic for food and beverage maintenance teams.
Maintenance technicians across the industry are highly specialised, with a great deal of specific technical knowledge and experience in using a large array of bespoke machinery that has to operate at a near-continuous pace. Stoppages in production can spiral unless they are dealt with effectively and expediently. With fine profit margins and high competition between manufacturers across the industry, not having enough highly skilled maintenance employees can be disastrous.
Manufacturers and plant managers, therefore, must have a system in place to allow them to get the most from their shrinking workforce. The system must be able to reduce the workload that maintenance teams need to carry out, letting them concentrate on fixing and maintaining machinery.
Right place, right time
Effective organisation and prioritisation while working with smaller teams is paramount to success. Teams that are spread out too thinly don’t have the manpower to deal with complicated fixes, yet concentrating all of your maintenance workforce in one place means they won’t be able to deal with issues in time. Achieving balance requires having a strong and in-depth overview of the complete maintenance system.
For example, maintenance teams should not lose precious time carrying out routine checks for processes that can easily be automated. While smart sensors have already reduced the workload for maintenance teams, having systems that can extract meaningful information from the captured data is also needed.
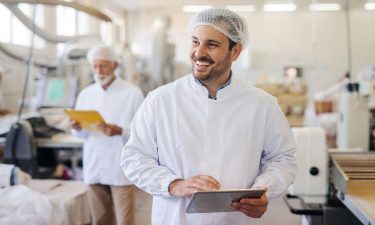
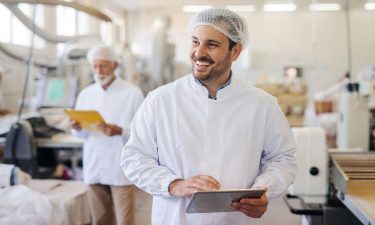
MOM systems will provide detailed instruction checklists which help workers be more efficient.
Manufacturing operations management (MOM) systems provide a detailed overview of facility health. This allows plant managers to plan, create and execute equipment maintenance tasks using predictive system observations. Deploying maintenance teams in this fashion will help protect businesses and production, even if the organisation is low on manpower. MOM systems also allow for the creation of task execution checklists for technicians, which means no job gets missed.
Consider, for example, a manufacturing plant with three conveyor belt motors that need fixing. Two are in separate areas of the same plant and one is at a completely different location. The MOM system will be able to rank which conveyor is likely to break down first and have the most impact, letting the plant manager deploy an experienced technician to the most critical motor.
The MOM system also provides detailed instruction checklists or maintenance manuals, which will help even the most experienced maintenance worker be more efficient. This also helps trainee technicians improve their skills with a library of information available at their fingertips.
The next steps
In terms of research and development, food and beverage is one of the leading industries because of its use of new, innovative technology. However, when it comes to maintenance, many companies still find themselves keeping paper records. While regulation and compliance requirements historically drove these companies to work with paper, advancements in digital tools mean this is no longer the case.
Unfortunately, once paper-based systems are in place, they can be difficult to eradicate. Companies become stuck in their ways, which leads them to ignore the significant cost savings, efficiencies and competitive advantages electronic systems can provide.
The most important driving force for a company’s success is its employees. Today’s maintenance engineers already have the computing knowledge to make the switch to digital. Providing them with a familiar interface that quickly connects employees across the organisation allows staff to work faster and smarter, increasing productivity. Electronic records also eliminate time-consuming and error-prone data entries that are common with paper-based systems.
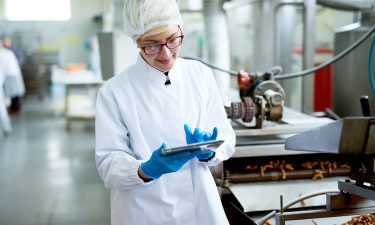
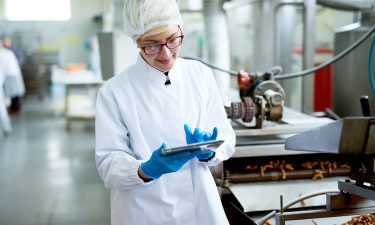
Maintenance staff can input data faster if they have access to mobile phones, tablets and other electronic devices on the factory floor.
While staff are the most important factor of any company’s success, the biggest cost of manual maintenance comes from people. It costs companies time and money to perform tasks that could be automated. Human errors that occur during manual record-keeping can also result in redundant actions, rework and audits. Electronic records also eliminate the costs associated with printing, reviewing and retrieving paper documents.
Giving maintenance staff access to mobile phones, tablets and other electronic devices on the factory floor allows them to input data faster and therefore gives them more time to spend completing tasks. Having a digital record of the machinery that regularly needs repairs also means that the engineer has easy access to the data when it is time for the next round of maintenance.
Augmented Reality (AR) is another example of technology that is increasing worker effectiveness. AR enables detailed overlays that can live-stream instructions to the technician, meaning that they can receive detailed instructions as they go. Many AR systems also film what the user is seeing, meaning more experienced technicians will be able to view proceedings and give advice, while recordings will likely become a key part of future training structures and allow for constructive review sessions.
Virtual Reality (VR) also has great potential for training. Digital models of real-world machinery and entire plants will allow technicians to test deconstructing, fixing and reassembling machinery without impacting the real equipment. Pairing these two technologies with the wealth of data and analysis provided by MOM systems will allow employees to understand their system effectively.
Engineer training
As digital processes and automation become more prevalent on the factory floor, the skills needed to be a maintenance engineer are expanding. Not only do engineers need to be able to use smart devices proficiently, they also need to be able to work alongside automation on a daily basis.
There is no standard certification or qualification needed to become a maintenance engineer, which has led to discrepancies in skills across the world. While education is important, plant managers should understand that each manufacturing facility is different and therefore invest in on-site training for all new engineers and regular updates for the entire workforce is vital.
Preventative maintenance
Once engineers are trained and maintenance records are easily accessible, plants can start to consider the impact of preventative maintenance on their operations.
Unplanned outages always seem to occur at the worst possible moment, whether it’s during high season or large batch production. These outages often lead to waste, as the product being made at the time of the outage often has to be disposed of. If it doesn’t lead to wasted product, outages will most certainly cause varying degrees of downtime, which not only causes production loss but can also lead to orders being cancelled and contracts being withdrawn if deliveries are not made on time.
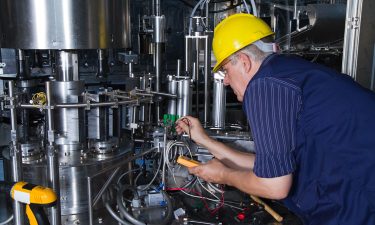
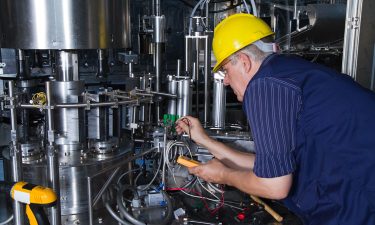
By taking into consideration potential problems on the production line, plant managers can reduce disruptions…
By taking into consideration potential problems on the production line, plant managers can reduce disruptions and help secure long-term competitiveness. All food and beverage manufacturers have periods where they are either not producing or producing much less than they are during the high season. This is the ideal time to be carrying out maintenance on the production line. If a plant manager knows that their motor is likely to need repairing annually, they can carry out the work during quiet periods, minimising the amount of downtime and lost production.
Overall Equipment Effectiveness (OEE) is a versatile measurement for production efficiency. It takes into consideration three factors – availability, performance and quality. Availability is reduced by equipment failure, setup and adjustment; performance is reduced by idling, minor stops and reduced speed; and quality is reduced by process defects and start-up losses. Research has shown that improving any of these factors will have a major impact on efficiency – and carrying out preventative maintenance helps improve all three by reducing equipment failure, stoppages and defects.
While the future of the UK engineering industry is still uncertain, it is not a reason to remain complacent when it comes to plant maintenance and managing a workforce. Just like when a motor is not performing as efficiently as it should be, the answer is never to sit on your hands and wait for a solution to appear. Plant managers need to grab the bull by the horns and plan for the future – it is this that will ensure the continuous operation of a plant and the industry as a whole.
Related topics
Equipment, Food Waste, Processing, Product Development, Recruitment & workforce, Research & development, Robotics & automation, Technology & Innovation
Interesting read Darcy and some great points highlighted! I personally believe the solution to this is Predictive Maintenance in the form of simple wireless remote monitoring IoT network sensors that monitor your assets on a 24/7 basis that alerts you in real time to any abnormalities it detects preventing costly damages and maximising up-time.
Thanks,