Chocs away at Barry Callebaut
- Like
- Digg
- Del
- Tumblr
- VKontakte
- Buffer
- Love This
- Odnoklassniki
- Meneame
- Blogger
- Amazon
- Yahoo Mail
- Gmail
- AOL
- Newsvine
- HackerNews
- Evernote
- MySpace
- Mail.ru
- Viadeo
- Line
- Comments
- Yummly
- SMS
- Viber
- Telegram
- Subscribe
- Skype
- Facebook Messenger
- Kakao
- LiveJournal
- Yammer
- Edgar
- Fintel
- Mix
- Instapaper
- Copy Link
Posted: 1 September 2014 | Barry Callebaut | No comments yet
Barry Callebaut recognised that a significant increase in operational efficiencies could be achieved through the installation of a robotic palletising system at its Banbury plant…
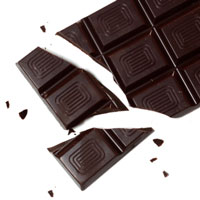
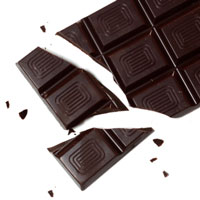
The Situation
Barry Callebaut, the world’s largest manufacturer of cocoa and chocolate products, recognised that a significant increase in operational efficiencies could be achieved through the installation of a robotic palletising system at its Banbury plant.
The company had recently initiated a major investment programme, in line with its ‘cost leadership’ strategy pillar, across all areas of its manufacturing process to deliver an increase in capacity and optimise production flow. To further improve efficiencies, a three phase investment over two years was now planned for the palletising area with the implementation of a fully integrated robotic solution to an existing line.
The new system was required to provide greater flexibility and reliability, utilise limited floor area, simplify operational procedures and reduce maintenance costs. In addition, it would have to overcome the challenges of picking up multiple sizes of boxes (between 10kg and 25kg), increased cycle rates and be fully compliant with the company’s stringent health and safety disciplines.
The Solution
Barry Callebaut commissioned CKF Systems of Gloucester as its project partner to design, build and install an integrated robotic palletising system within its manufacturing plant.
“We were impressed by work CKF had recently undertaken for a major confectionary brand,” explains Barnz Parkin, Project Management Engineer, Barry Callebaut. “We spoke to the project manager, who has a wealth of experience and we regard highly and he provided a sound endorsement; a good partner, talented, flexible and reliable.”
“We looked at nine different organisations, only CKF demonstrated a complete understanding of our situation and submitted a working solution that would improve our capabilities in line with budget and expectations. It was a major undertaking for the business and therefore essential that we made the right decision.”
The initial project is designed around a single robot cell but with the ability to palletise three different SKU’s at the same time. The cell, incorporating an ABB IRB 660 with a bespoke gripper, has been designed by CKF. It utilises 3D Inventor and Robot Studio simulation to ensure the full range of case sizes, weights and configurations can be handled and are able to pick layer sheets. The case feed system comprises a high level interface complete with divert station and bar code detection, to direct the flow of designated cases to the robot cell and separate in to three defined collation stations. Each station incorporates an identical conditioning section to orientate and collate the cases into defined rows and counts for the robot pick to create the pallet pattern. A dedicated pallet load station is positioned at the end of each collation station and the cell also includes two separate layer sheet feed sections to handle both Chep and Euro pallet sized sheets.
The overall system includes two dedicated pallet denesters, i.e. Chep and Euro, loaded pallet discharge station and twin shuttle car. The shuttle car arrangement is designed to receive individual pallets, on demand, from the designated denester and deliver to the relevant pallet load station at start of production. The shuttle is also designed to receive and exchange both loaded and empty pallets, with the loaded pallets delivered to the unload station before the car returns to the denester stations to collect the next pallet. The final configuration of the system includes provision for the introduction of a second robot cell and a fully automatic spiral wrapping machine.
The complete operation is fully contained within a guard enclosure incorporating strategically positioned light beams, roller shutter door and interlocks to meet the very highest safety standards with zoned safety areas to maximise overall system efficiency.
“We are delighted by the initial results and the mindset shown by CKF. Our decision has been vindicated,” explains Chief Engineer Mike Parkins. “There is total professionalism in the way their engineers see and do things; CKF understands our business and the very high standards we demand.”
“We attached great importance to maintaining scheduled output without disruption and CKF ensured that during installation and commissioning our existing machine continued to pack at all times. There was a close collaboration throughout between CKF’s engineers and our own team, ensuring that when it was necessary to break into the line this was done with minimal disruption.”
The Benefits
The project was fully operational within six months of placing the order and significant benefits have been achieved from the investment. Reliability has increased and the capability of the single cell has more than doubled, from 300 to 700 cases per hour.
“The new line fits perfectly with our long term capacity-increase model,” concludes Mike. “It’s easy to operate, requires minimal maintenance and reinforces the company’s commitment to improving health and safety. Investment in robotic and automation applications is fundamental to our future, improving efficiencies whilst reducing the environmental impact.”
Barnz Parkin praises the work undertaken by CKF Systems and the smooth transition to a fully automated operation.
“I have been impressed by CKF’s flexible approach along with high levels of thought, care and detail. The onsite engineers were professional throughout, even a series of last minute demands were handled extremely smoothly.”
“CKF has demonstrated a willingness to understand our working practises and work closely alongside our own staff. Not only has this ensured a healthy team spirit, our work force immediately bought into the changes and the ongoing training programmes. Everyone now recognises the long term benefits and there is an excitement relating to these new technologies. I have been installing production lines for many years in various countries throughout the world and without doubt my experience with CKF has been one of the best. I’d not hesitate to employ them again.”