KP Snacks’ tool control takes food safety to another level
- Like
- Digg
- Del
- Tumblr
- VKontakte
- Buffer
- Love This
- Odnoklassniki
- Meneame
- Blogger
- Amazon
- Yahoo Mail
- Gmail
- AOL
- Newsvine
- HackerNews
- Evernote
- MySpace
- Mail.ru
- Viadeo
- Line
- Comments
- Yummly
- SMS
- Viber
- Telegram
- Subscribe
- Skype
- Facebook Messenger
- Kakao
- LiveJournal
- Yammer
- Edgar
- Fintel
- Mix
- Instapaper
- Copy Link
Posted: 11 January 2016 | Victoria White | No comments yet
KP Snacks has announced that it has introduced Snap-on tool management onto its production line…
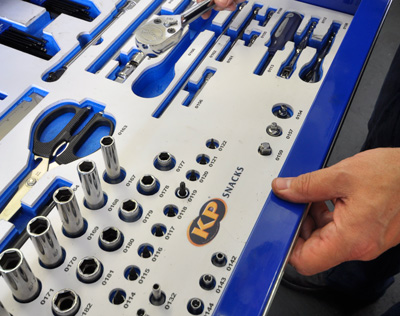
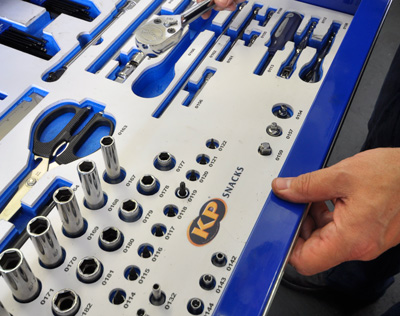
With new legislation and tighter controls on health and safety, KP Snacks has announced that it is taking food safety to another level, with the introduction of tool management onto the production line.
Whilst KP Snacks had multiple tools on the factory floor, there was no system in place to track specific tools or carry out audits.
Jeremy Derbyshire, Site Director at KP Snacks explains: “For KP Snacks, tool control was very much an embedded standard in industries such as aviation but very few suppliers had made the crossover into the food industry. The food safety of our products is of paramount importance to KP Snacks and we take every step possible to safeguard our consumers, constantly challenging ourselves to improve and exceed our customer requirements.
“Researching the market, the same name kept coming up as market leaders in tool control: Snap-on Industrial. The company has a solid track record in dairies and an understanding of the challenges that food manufacturers face when it comes to tool control.”
KP Snacks started working with tooling solutions specialist Snap-on Industrial in 2013, initially gaining an understanding of the way it could control and manage its tool system within its manufacturing sites.
KP Snacks signed up to Snap-on’s Level 5 NTC (Networkable Tool Control) system. This offers staff the opportunity to manage a virtually unlimited number of lockable tool storage units simultaneously for complete system control. It also allows tools and assets to be controlled in real-time, reducing the risk of foreign objects in food.
The keyless entry allows authorised staff at KP Snacks access to the tools they need, while the operating software within the NTC system tracks access based on employee ID key cards. All tools are serialised and linked to a specific toolbox via laser etching. The NTC system enables the user to report tool events such as being lost, broken or away to calibration (and other locations) directly at the toolbox. This information, plus toolbox access records, is stored within log files on the toolbox and can be viewed or printed at any time. This provides a full audit record of toolbox access (or declined access) by user, time and date and a complete history of tools with events marked against them such as being lost or broken.
Snap-on’s solutions gave KP Snacks the level of customisation they required
Gareth Dughan, Engineering Manager at KP Snacks and responsible for the tooling project, explains why an easy to use, real-time tooling system was so important: “Each area of our factory requires different tools so we found that we needed to tailor the tool inventory to each specific area. The level of customisation Snap-on provided allowed us to make this project more cost effective by ensuring that we only purchased the tools needed for a certain area, thus avoiding unnecessary and costly duplication. We were also impressed by the laser etching service that ensured that each individual tool could be identified to further improve our traceability.”
This has produced important time savings for the staff on the production line, explains Gareth: “Producing an inventory of tools every day wasted precious time with over 100 members of staff spending up to 15 minutes a day managing their tools across three shifts. Using Snap-on meant we were able to manage our time better and the NTC system has helped make the process seamless.
Jeremy concluded, “The tool chests have enabled us to easily demonstrate that, when it comes to the safety of our products, we are willing to invest in the very best solutions available. Food safety and compliance has continued to improve across our factories and our factory floors have benefited from having all the tools in easily accessible storage units.”