Hygienic steel belts for food processing
- Like
- Digg
- Del
- Tumblr
- VKontakte
- Buffer
- Love This
- Odnoklassniki
- Meneame
- Blogger
- Amazon
- Yahoo Mail
- Gmail
- AOL
- Newsvine
- HackerNews
- Evernote
- MySpace
- Mail.ru
- Viadeo
- Line
- Comments
- Yummly
- SMS
- Viber
- Telegram
- Subscribe
- Skype
- Facebook Messenger
- Kakao
- LiveJournal
- Yammer
- Edgar
- Fintel
- Mix
- Instapaper
- Copy Link
Posted: 18 April 2016 | Berndorf Band GmbH | 2 comments
There are now a wide range of technical processes in food production upon which the means and manner of the conveying has an impact…
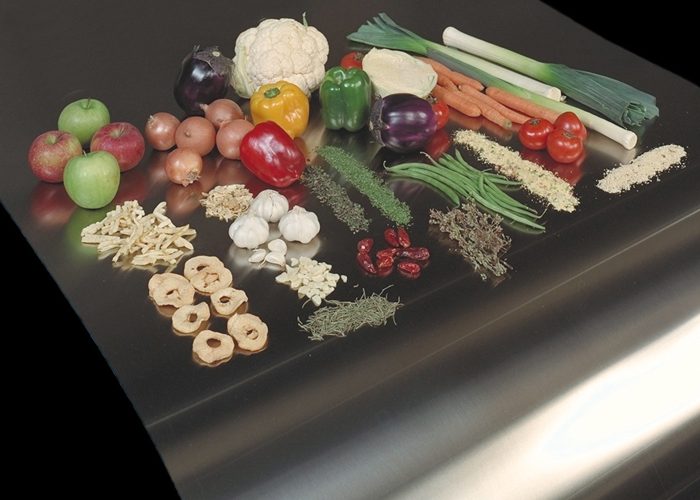
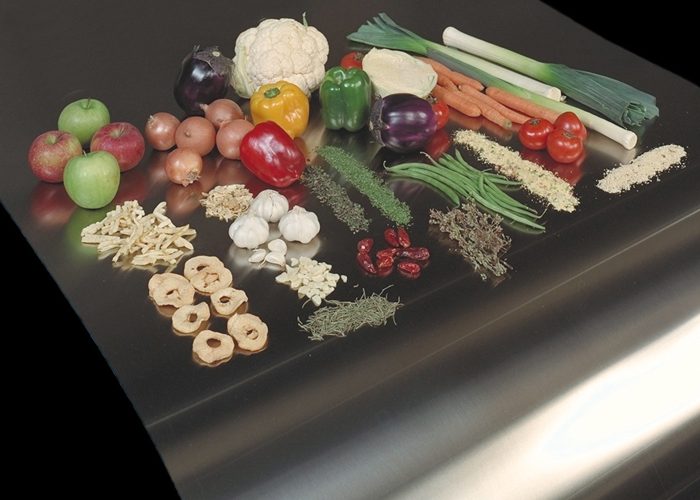
Cooling, deep-freezing, steaming and drying are now-a -days standard on-line processes. There are several alternative systems for conveying the products to and through these stages and each have their benefits. The food industry is very conscious of strict hygienic requirements and as a result products offering high hygiene benefits, such as endless stainless steel belts, are considered to be an important option.
Process Applications
The resilience and hygiene benefits of steel belts make them attractive to a broad number of food processing sectors. The intrinsic characteristics of steel include unique physical benefits. Steel belts are extremely good conductors of heat or cold. When conveying into, through or out of cooking, chilling or freezer processes steel offers efficiencies of more rapid heat or chill transfer. Stainless steel belts can be perforated for drainage in high moisture areas or to increase temperature transfer in baking ovens for example.
The meat, poultry and fish industries are installing these conveyors especially where cut, raw product is being conveyed in chill environments. The bakery industry values the flatness and uniform dark heat absorbing surface, ensuring energy efficiency. CARBO 13 steel belts can easily handle operating temperatures of up to 400° C.
Hygiene aspects
In the meat processing industry for example the smooth surface of steel belts avoids the lodging of fibres or fat remnants during processing because there are no gaps.
Even if such deposits are not pathogenically contaminated they can provide a refuge and source of growth materials to bacterial deposits from subsequently contaminated meat or from environmental bacteria. A minimising deposit opportunity is therefore important.
Whatever the level of deposit it needs to be completely removed at regular intervals and this can require the use of a combination of energetic systems such as pressure washing and some chemicals that can be considered to be aggressive and environmentally damaging.
This can be a significant factor in choosing a conveying system. The fact that steel belts from Berndorf Band not only meet strict hygienic requirements but are also easy to clean is seen as major advantage. The smooth steel belt surface needs less chemicals and less water than conveying systems using modular construction to achieve the required level of hygiene. The cleaning area can be reached easily and there are no hidden edges.
The fact that cleaning is mush easier not only reduces the consumption of water and cleaning materials it reduces the time required to complete. It can also reduce the need for re-cleaning when rapid hygiene tests show a red warning. There are opportunities for savings on cleaning labour costs.
Strong & precise
The dynamic strength of continuous steel belts is a major factor in selection because all types of conveyor belts have to be in endless operation and a conveying breakdown can have a significant impact on down time. To the general stress of continuous running the process stresses of heat and / or cold have to be added. Therefore the thermal stability, hardness and chemical resistance properties of steel belts are attracting a large amount of interest.
Wear and tear and corrosion resistance is another crucially important benefit of steel belts. Therefore, Berndorf Band pays special attention to the selection of material and to the manufacturing method. During each production step all steel belts are run in endless condition between two drums. The results of this production method are perfect tracking and best belt straightness. For a customer this means less down time resulting from tracking problems and longer belt life due to less belt damage.
Vee-ropes and product retaining strips
Traction control and product retention are critical for certain products and processes and steel belts can be supplied with vee-ropes and / or product retaining strips. A special bonding method ensures perfect adhesion of within operating temperatures ranging from -60° C to + 100° C. Nitrile rubber is used as a standard material.
For low temperature applications and for retainers with indirect contact with processed foods, Berndorf for example would recommend using natural rubber. Retaining strips for bake oven belts however are made from silicone rubber and this need to be bolted onto the steel belt.
Technical support
The resilient and reliable performance of steel belts is such that they require a low level of service than more complex systems. Berndorf Band has an international service network offering steel belt installation, repair and inspection. The unique characteristics of steel belts call for highly qualified engineers and service technicians who can perform inspections.
Furthermore Berndorf Band offers special engineering services related to conveyor improvements. This leads from conception to delivery and installation of conveyor components such as skid- and graphite bars, idler rollers or belt cleaning elements. A further example of such comprehensive service is the adjustment of steel belts and all belt touching parts in order to ensure good belt tracking that increases the life cycle of steel belts and minimizes down time.
Very important to keep hygienic the methods for which we process our foods. Using magnets to remove excess particles and metals as well as keeping everything in tip top hygienic condition are ways we can ensure consumer safety when it comes to consumption.
A fantastic new approach to food hygiene, just fascinating!