Do you need a magnetic separator or metal detector?
- Like
- Digg
- Del
- Tumblr
- VKontakte
- Buffer
- Love This
- Odnoklassniki
- Meneame
- Blogger
- Amazon
- Yahoo Mail
- Gmail
- AOL
- Newsvine
- HackerNews
- Evernote
- MySpace
- Mail.ru
- Viadeo
- Line
- Comments
- Yummly
- SMS
- Viber
- Telegram
- Subscribe
- Skype
- Facebook Messenger
- Kakao
- LiveJournal
- Yammer
- Edgar
- Fintel
- Mix
- Instapaper
- Copy Link
Posted: 3 April 2017 | BUNTING Magnetics Europe Ltd | 2 comments
5 key questions to ask before making a decision…
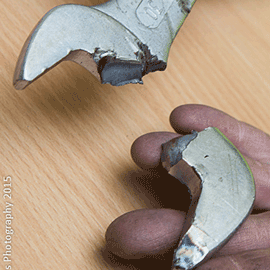
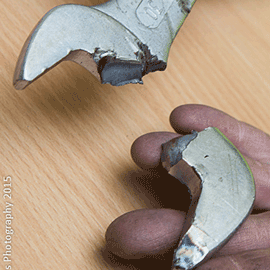
There is a metal contamination issue that needs addressing and the conclusion is that either a Magnetic Separator or a Metal Detector will solve the problem. So, before a purchase is made, what key questions have to be asked?
- Why is the metal contamination an issue? This may sound like an odd question, but why has this issue suddenly become a burning problem? Is it because the metal has damaged other equipment or is it because the metal has ended up in the end product either just before or after being supplied to the customer?
- What and how big is the metal contamination? Metal contamination can occur in many forms:
- Large sized metal items include spanners, screwdrivers, broken pieces of other equipment and even mobile phones;
- Medium sized metal items include nuts, bolts, nails and pieces of damaged pumps,
- Small metal such as shards from a broken screen, pins and fragments from worn equipment;
- Fine and very fine metal contamination that occurs from worn processing equipment, especially when processing hard materials such as cocoa beans;
- Is the metal magnetic or non-magnetic? Oddly enough, some ‘non-magnetic’ metals such as stainless steel can become very weakly magnetic if they are work hardened. The edges of stainless steel bolts are often weakly magnetic, as is fine stainless steel originating from the wear of processing equipment;
- What is the extent of the metal contamination issue? Very often the issue will only be raised when either a customer complains, a key item of processing equipment is damaged or a batch of product is rejected by internal quality control. However, finding such metal contamination once means that it is highly likely that there is metal passing through the system undetected;
- How much does and could the metal contamination problem cause the business? Sometimes this is difficult to calculate as how much is a damaged reputation worth? If an item of equipment is damaged, then it is easy to put a figure on the repair or replacement cost, but what about lost production and the associated labour costs?
So as to the original question, the answer is that it is highly likely that both a Magnetic Separator and Metal Detector will be required, located at different points within the process for very specific objectives.
For more information or a site review by our trained sales engineers, please contact us on:
Phone: +44 (0) 1442 875081
Email:[email protected]
Via the website
I think many people let metal contamination go unnoticed – more than we really think. It is important to consider the health of our consumers in the highest regard when it comes to producing food goods, so if even for just a safeguard it would be a great idea to purchase a magnetic separator.
Great post! Those are all very important questions to ask when dealing with metal contaminants, and not something you necessarily think about when discovering such a contamination. Magnetic separators are always a great preventative measure!