TOMRA to highlight the benefits of its sorting and grading technologies at Asia Fruit Logistica 2019
- Like
- Digg
- Del
- Tumblr
- VKontakte
- Buffer
- Love This
- Odnoklassniki
- Meneame
- Blogger
- Amazon
- Yahoo Mail
- Gmail
- AOL
- Newsvine
- HackerNews
- Evernote
- MySpace
- Mail.ru
- Viadeo
- Line
- Comments
- Yummly
- SMS
- Viber
- Telegram
- Subscribe
- Skype
- Facebook Messenger
- Kakao
- LiveJournal
- Yammer
- Edgar
- Fintel
- Mix
- Instapaper
- Copy Link
Posted: 30 August 2019 | TOMRA Food | No comments yet
TOMRA Food, Compac and BBC Technologies to showcase advanced sorting, grading and packing solutions at Asia Fruit Logistica 2019.


The InVision2 TotalView.
TOMRA Food, Compac and BBC Technologies will showcase their advanced sorting, grading and packing technologies at Asia Fruit Logistica 2019, which will take place from 4-6 September in Hong Kong.
The three companies will be exhibiting together at Hall 5 Booth N20, where Compac will unveil InVision2, the new cherry grading platform that takes cherry grading and sizing accuracy to a new level.
TOMRA’s three pillars: technology leadership, food trust, and digital transformation
TOMRA Food’s presence at the exhibition with Compac and BBC Technologies will highlight how the technology leadership of its unique offering enables producers to improve accuracy, efficiency and yields, while ensuring high standards in food quality, hygiene and traceability – and reducing food waste.
The result is produce that is accurately graded and safety-assured, packed efficiently and handled with extreme care. And through digital transformation, data analytics are optimising machine efficiency, reducing operational costs, and assisting food traceability. For the producers this means establishing food trust, safeguarding their reputations and enhancing their economic performance.
Compac raises the bar on cherry grading and sizing accuracy with new InVision2
Compac will present its new cherry grading platform, InVision2, which delivers the most accurate cherry sizing and grading performance on the market today. It retains its predecessor’s industry-leading five views of the fruit and raises the bar on detection of fine defects, such as stem pulls, bruising, sutures, small scarring and other small-size blemishes.
It features ultra-high-resolution optics for the detection of fine blemishes, while new LED lighting provides greater illumination of each cherry. It also introduces an all-new compute and electrical system which provides a step-change in performance and a platform for future software releases to deliver further improvements over time, so that InVision2 will grow and evolve with the customers’ requirements.
With these improvements, InVision2 delivers the most accurate and stable sizing, resulting in higher value packout. The extremely accurate defect grading with low good-in-bad (GIB) enables consistent throughput irrespective of fruit quality, and maximises yield and returns for the packhouse and grower. The greater precision of the system also reduces the operators’ workload, to the benefit of the overall operation. InVision2 is supported by Compac Care, the service program that ensures the customer’s equipment is ready on day one and runs optimally throughout the cherry season.
InVision2 can be further enhanced with the TotalView module to provide seven views, delivering the only system capable of true 100 percent surface inspection of the cherry at true production speeds. The positioning of the TotalView cameras at a low angle ensures optimal coverage of the cherry stem bowl or nose, critical areas where defects have previously been difficult to detect. This unique field of view enables InVision2 TotalView to deliver the clearest and most complete view of the cherry available on the market. By offering TotalView as a module, customers have the option to upgrade their operation as their business develops and they seek to further automate their packing line and reduce weather-related risk.
Prototype testing of InVision2 was completed at Prima Frutta, California’s premier supplier of cherries and apples. The system was tested thoroughly in the very challenging 2019 Californian cherry season with very positive sizing and blemish improvements. As a result of the performance and return on investment, Prima Frutta has decided to expand its operation’s capacity with 32 new InVision2 TotalView lanes, and upgrades to all existing lanes.
Fruit Sensor Lab offers first-hand experience of state-of-the-art sensor technologies
Visitors to the booth will be able to view detailed reports on fruit’s internal and external quality and characteristics in great detail at the Fruit Sensor Lab. The inspection, which will use Tomra Food’s latest sensor technologies, such as Compac’s Spectrim and Inspectra platforms, will reveal more characteristics than is possible with older technology, including sweetness level, internal defects, storage capability, and hard-to-see subtle external defects.
The experience will demonstrate the power and possibilities of today’s advanced grading platforms and software algorithms.
BBC Technologies: peace of mind from the world leader in single provider turnkey solutions for small, delicate fruit
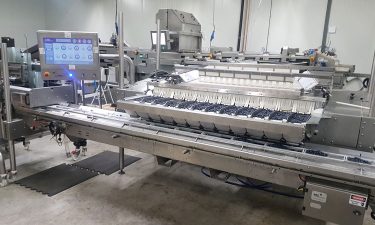
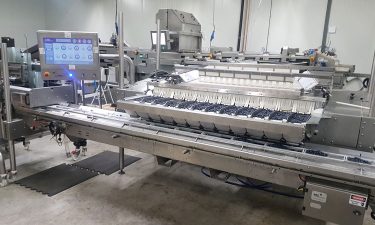
The CURO 12.
BBC Technologies will highlight the benefits of its world-leading complete turnkey solutions for sorting, optimising and packing small fruit, and its ability to develop turnkey solutions that are specifically designed to meet the needs of individual customers.
The company’s suite of advanced turnkey technology for fresh product offers optical sorting solutions such as the MIRA360™ machine which sorts cherries and small tomatoes for colour and identifies and removes defects including cracks and splits, soft rot, wrinkles and bruises and insect damage, and the KATO 260 blueberry grader which identifies defects down to 0.1mm while ensuring product is handled gently. Its versatile filling and packing solutions, designed with particular focus on speed, handling and accuracy, offer a choice of systems to match different customer requirements: CURO 2, CURO 8, CURO 12 and CURO 16 featuring 2, 8, 12 and 16 filling stations respectively, and box filling.